Select a Picking Technology to Drive Productivity Gains
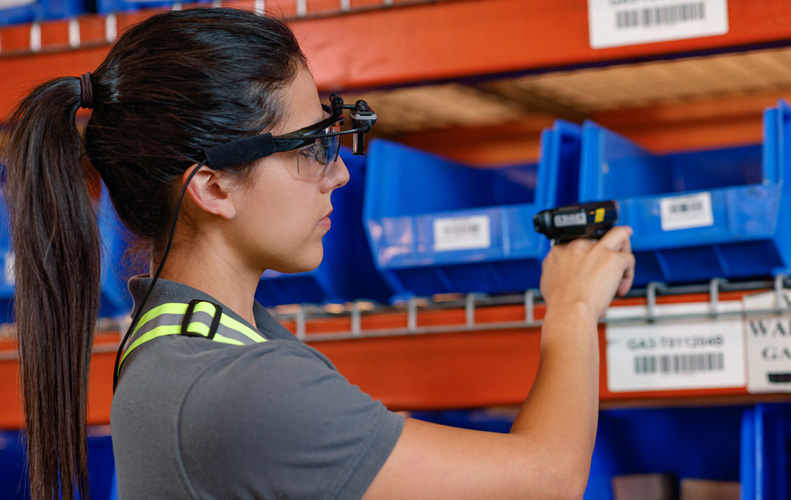
Learn about various order picking systems and how they improve productivity, increase picking efficiency and reduce labor costs in warehouse operations.
Modex 2020 is Here – What to Expect
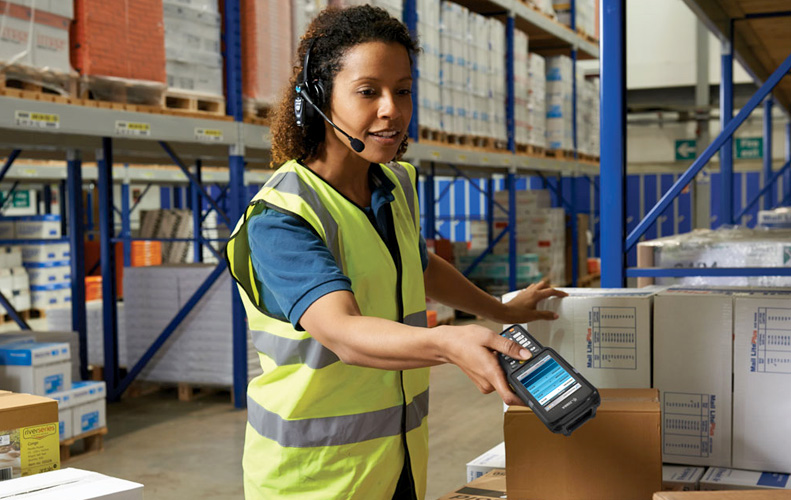
As a leading material handling and order fulfillment automation integrator, Numina Group has been designing and implementing more efficient distribution centers that provide clients more profitable operations for over 30 years. A design with leaner processes enforced with the right blend of automation technologies streamlines the entire order fulfillment operation to lower labor costs, increase accuracy…
How to Automate Pack and Ship Labeling Operations
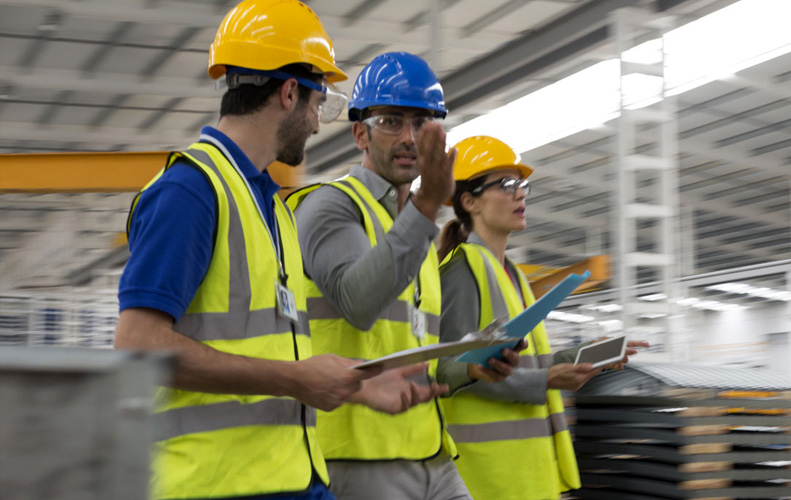
Pack and Ship Automation is a top consideration when investigating means to modernize and optimize order flow in a distribution center. Investing in a solution that blends the right mix of automation technologies -including weight and vision audit, carton dimensional measurement to automate manifesting, and the application of the packing sheets and shipping labels- are…
How Numina Group’s Automated WES-WCS Empowers Your Operations
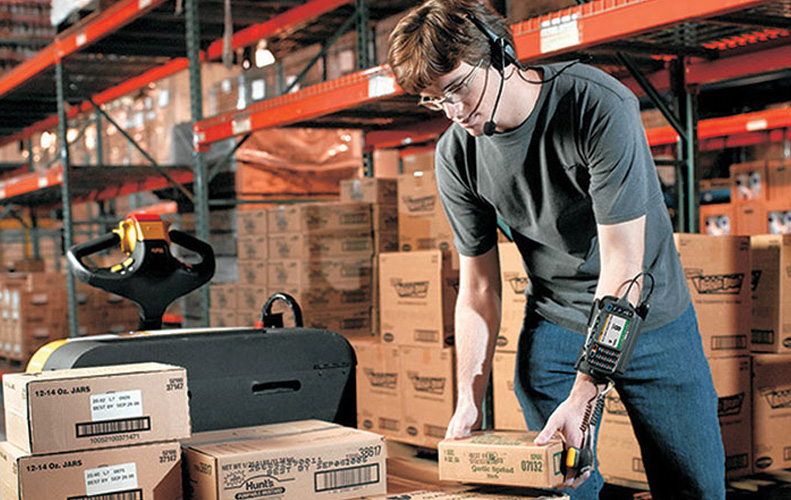
Order fulfillment labor costs are the largest cost in an e-commerce operation. In order to remain profitable, it is imperative to keep these costs in check. We are committed to developing and delivering solutions that lower our clients’ cost per order goals. Numina Group empowers more productive distribution operations with optimized processes and automation technologies…
The Right Voice Picking Solution Eliminates Shipment Errors in Your DC
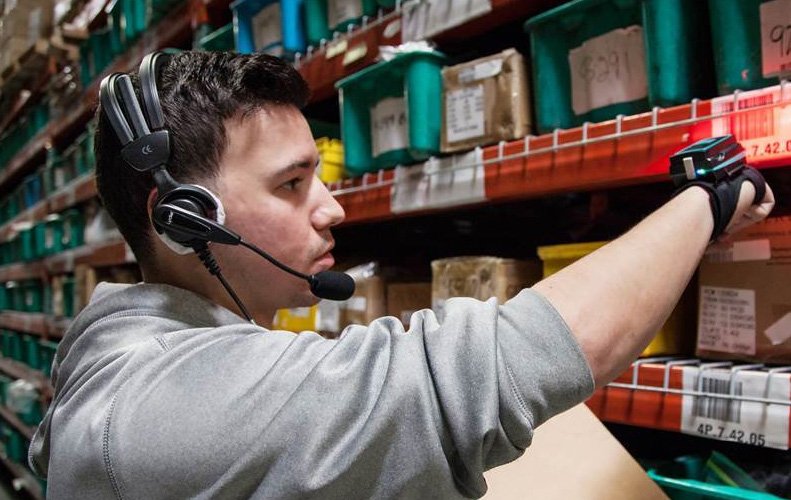
You see a watch online. You buy it. You select next-day shipping and pay ten dollars extra. Your watch arrives three days later…and it’s the wrong color! When that scenario happens, it frustrates customers and diminishes repeat purchases. Research estimates that the costs of miss-picks can drain profits of $400,000 per year from an E-com…
Automation Solutions to Eliminate Warehouse Constraints
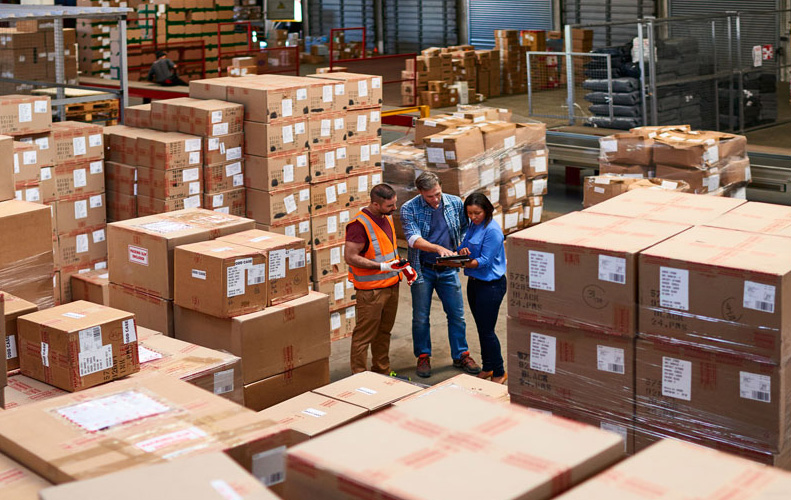
Technology is changing distribution operations to meet the demand of customers wanting faster services/shipments. According to research conducted by Invesp Co., 96% of customers associate fast as same-day delivery, so faster speed in the order fulfillment operations is essential. Moreover, faster operations impact customer loyalty. For example, according to a consumer study conducted by Oracle…
Benefit from the GO Zebra Trade-In Program with Numina Group

We’re excited to announce our recent partnership with Zebra Technologies, the industry’s leading mobile device automation manufacturer. Together our warehousing automation teams are implementing the latest technologies to manage better processes, boost operational efficiency to reduce labor costs, and increase order completion times and accuracy. One example of this is Numina Group’s real-time voice picking…
Peak Season is Done, but Your Warehousing Constraints Persist
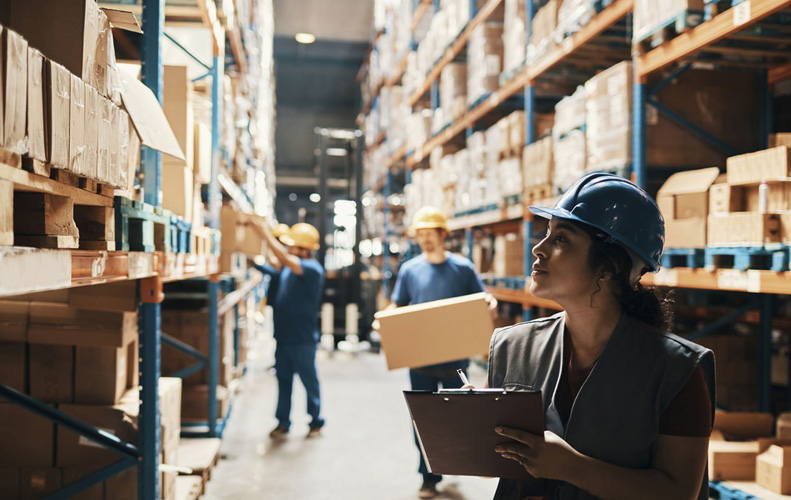
As expected, the 2019 holiday season shattered previous sales marks, ushering in nearly $720.3 billion, of which $9.4 billion came solely from Cyber Monday shopping through distribution giants such as Amazon and Walmart. While it will still take time to calculate the precise number of holiday profits, businesses nationwide must also be aware of the…
How to Achieve the Highest ROI in a Warehouse Automation Investment
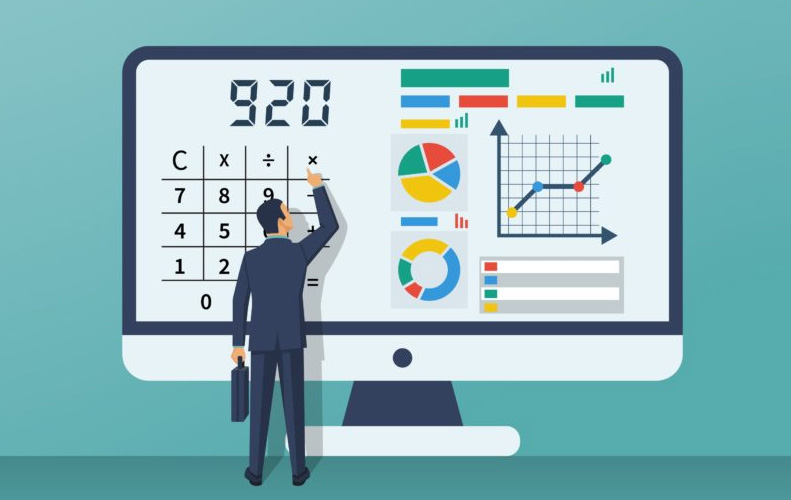
Before embarking on a large scale initiative most businesses want to determine the return on investment, “ROI”. There needs to be a detailed analysis performed prior to starting the project to understand the financial savings and the operational improvements that are the critical reasons a firm is investing in automating the order fulfillment process, such…
Seven Steps to Prepare for Peak Season
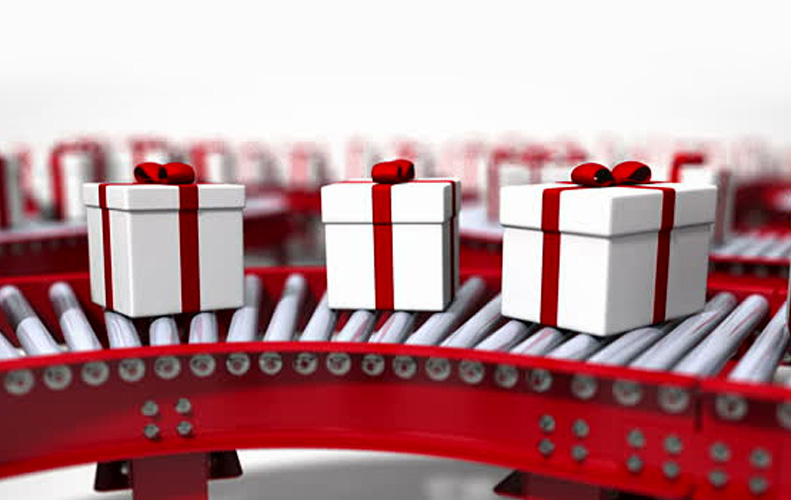
Have you walked into a retail store recently and noticed that the Halloween decorations are already in full swing? Some retailers are beginning to display Thanksgiving décor, so Christmas decorations are right around the corner! If you’re thinking hey, it’s only September, you are already behind the curve in preparing for peak shipping season.