Benefits Gained from Mobile Powered Carts
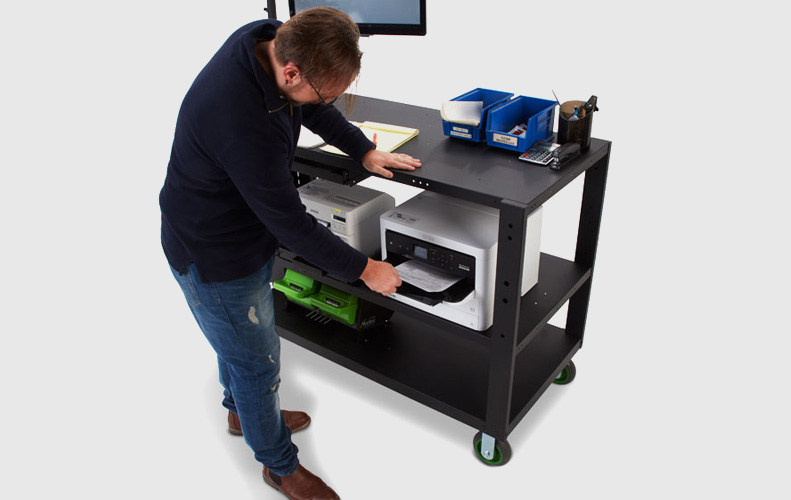
Sometimes simpler is better. This blog explores how mobile powered carts can be a very efficient solution for improving warehouse productivity and increasing throughput.
Mobile Powered Workstations & Carts
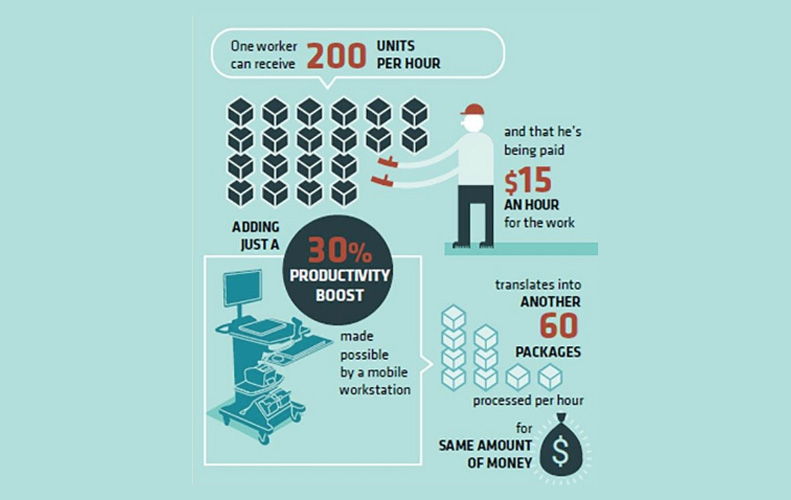
With so many technologies to automate and streamline warehouse operations, it can be easy to overlook how a lean simple technology can be combined with other technologies to reduce labor. Learn more.
8 Steps to Prepare your Omnichannel DC for Peak Season
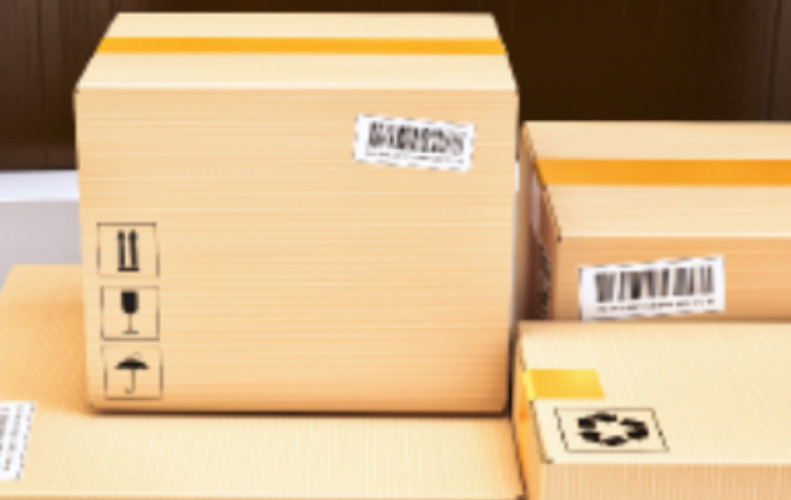
Re-working omnichannel fulfillment to prepare for increasing e-com orders may seem like an insurmountable challenge, but we’re here to help. Schedule a “Brainstorming Zoom Meeting” with one of our application experts.
Road Map to Lean Optimized Distribution Processes
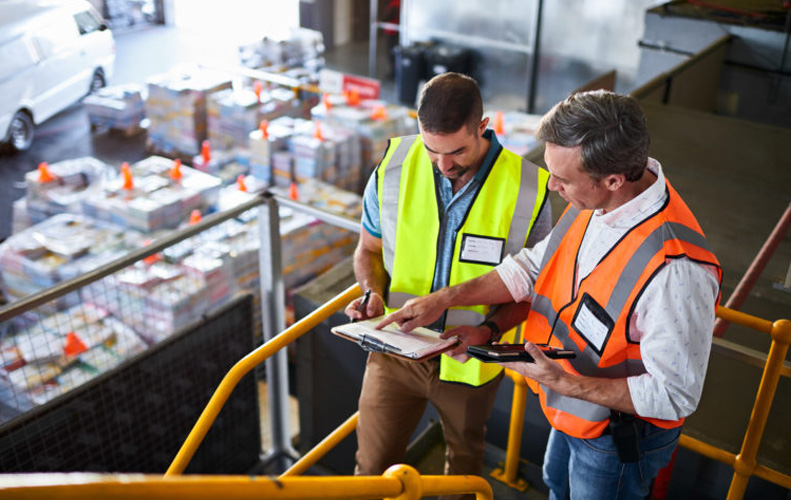
CNBC reports that due to the ecommerce boom the U.S. may need another 1 billion sq ft of warehouse space by 2025. ProLogis estimates that e-commerce companies require 1.2 million sq ft of distribution space for each $1 billion in sales. Clearly, the US and…
Considering Warehouse Robotics?

In 1961, Alan Shepard USA & Yuri Gagarin made the first manned flights into space. Another significant technological in 61’ also revolutionized manufacturing. This was the year General Motors brought the first Unimate robot, invented…
Selecting DC Automation for E-Commerce
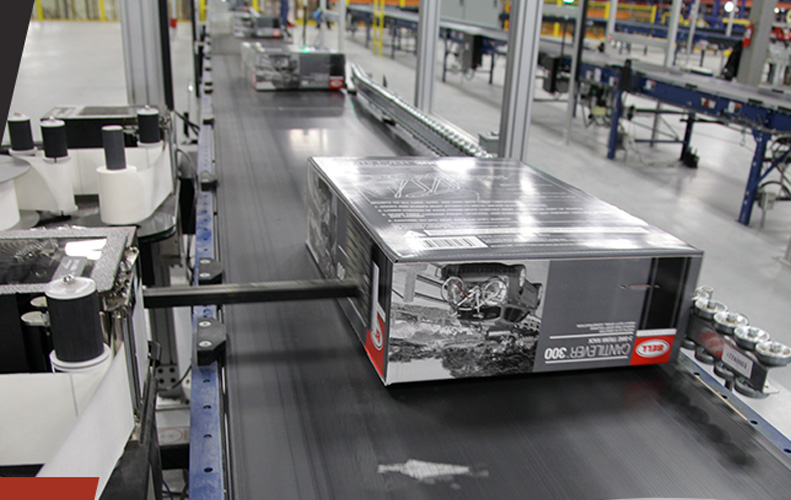
We’ve seen a big uptick in interest for process and technology improvements in many industries to streamline e-commerce order fulfillment. Learn more.
Warehouse Productivity and Technology Advancements
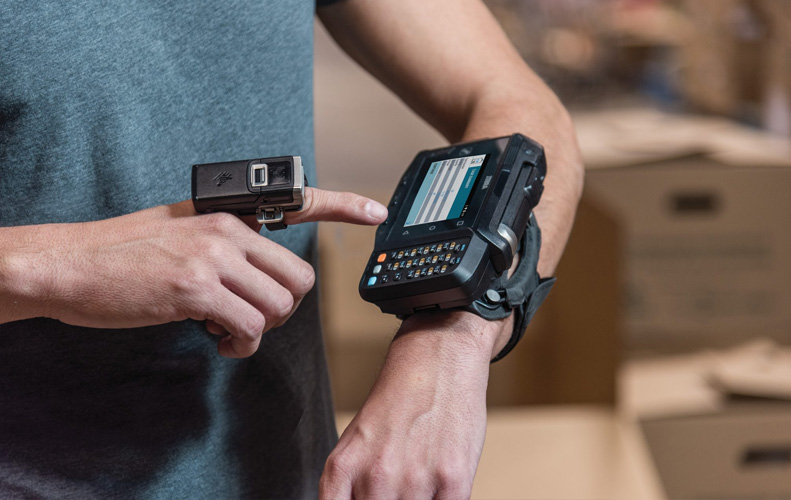
Refresh your knowledge on warehouse technology advancements that are now light years ahead of first-generation picking technologies! Learn more.
Balancing Work Across Multiple Pick Zones
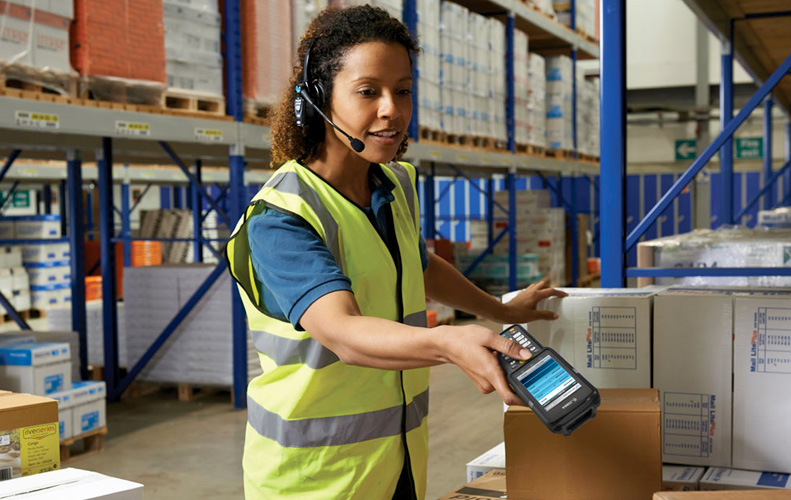
Learn how RDS™ Order Release Module balances the order mix across the split case and full case pick modules along with the order flow to the pack area, print-and-apply labeling, sortation and pallet build operations.
How to Navigate Business Disruptions with Collaboration Tech Tools
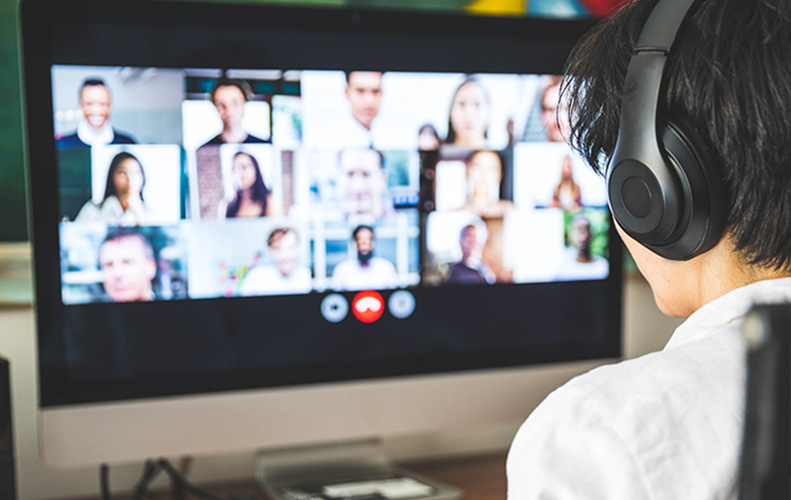
In the face of business disruptions, here are some ways to keep business moving forward – using tech tools that don’t require a major investment or require advanced training.
How Automation Intelligence Improves Order Fulfillment Efficiency
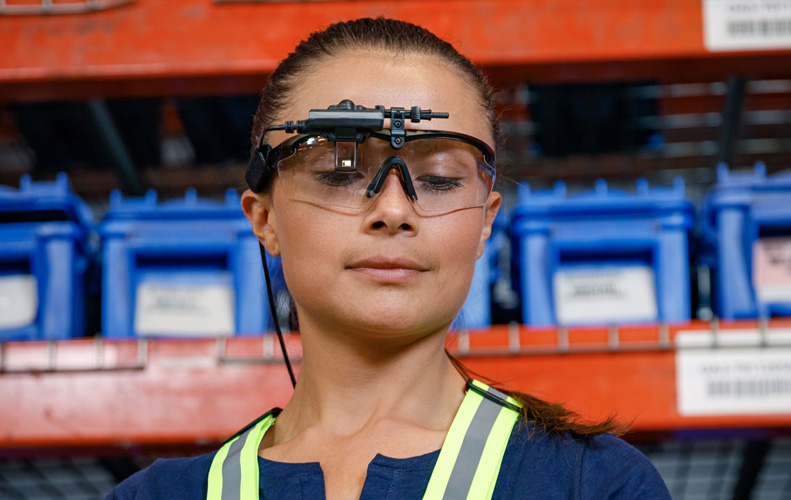
We have been fielding inquiries from interested customers regarding the impact machine learning and Automation Intelligence can have in the material handling industry, and how these concepts actually relate to real world distribution operations. This blog will give you a brief overview, but don’t hesitate to give us a call anytime to discuss these concepts…