The Numina Group’s New Cartonization Software Reduces Order Fulfillment Costs
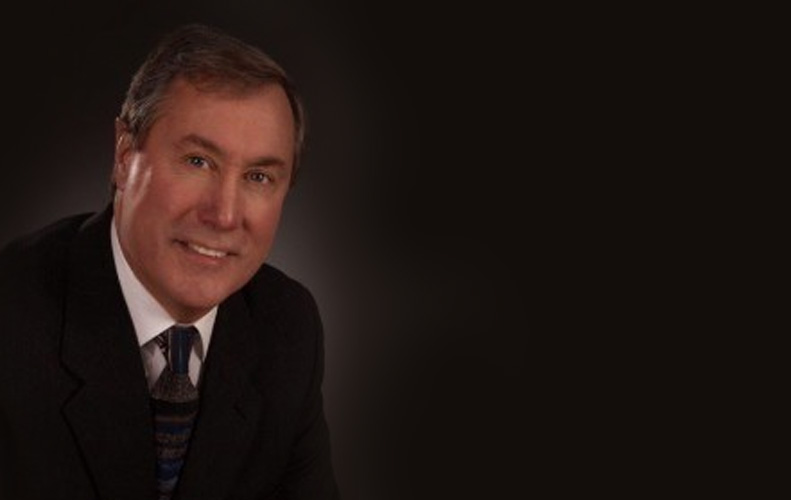
Numina’s latest software release combines cartonization logic and in-motion dimensional pick verification to lean up the picking…
Numina Group Debuts Latest Automated Pack and Ship Technologies at ProMat 2015
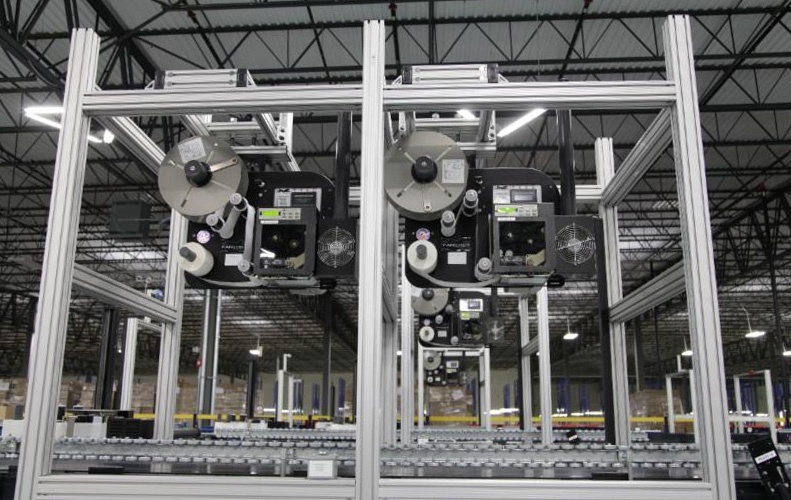
Numina Group will release the next generation of their patented One-Step Plus™ and X-Press PAL™ pack and ship…
Sunstar Selects Numina Group’s Omni-Channel Order Fulfillment Solution to Automate its New Schaumburg IL North American DC Operation
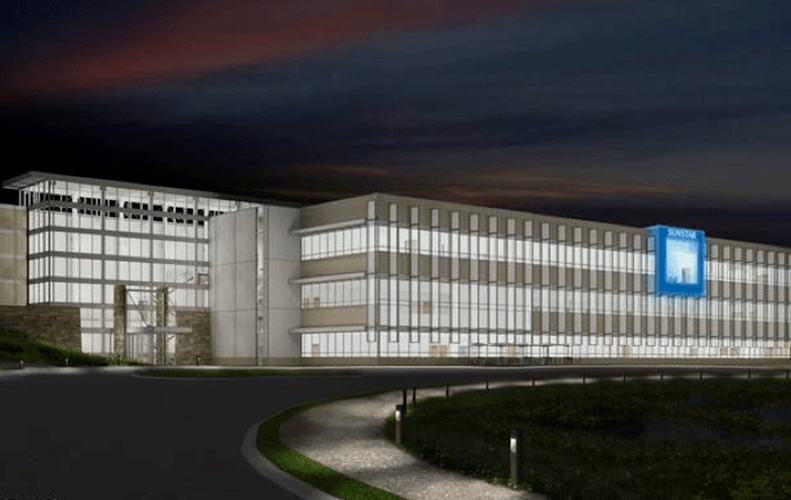
Numina Group’s RDS™ Warehouse Execution and Control Software, Voice-Directed Order Fulfillment to Increase Order …
Ferretto Group and Numina Group Announce Industry’s First Voice Directed Vertical Storage Units for Picking Automation at Promat 2015
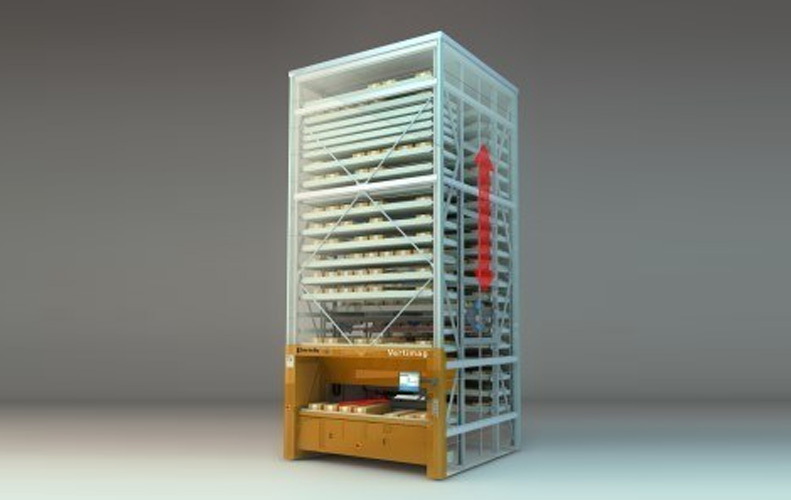
Numina Group’s RDS™ Voice is an integral component of the vertical storage inventory management and control software increasing the speed and accuracy…
Numina Group Debuts Latest In Automated Packing Systems At 2014 Pack Expo Show
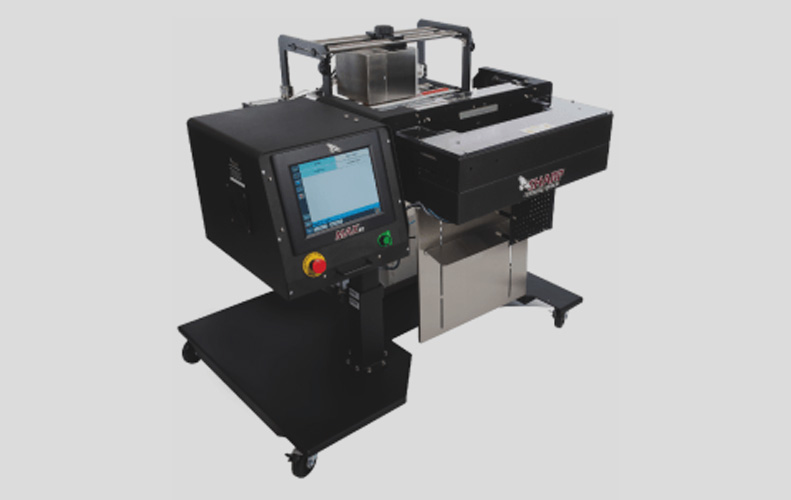
Numina Group’s RxPACK automated packaging system for mail-order pharmaceutical fulfillment will be showcased in Sharp Packaging…
MMH Details New Omni Channel Distribution Center At BRG Sports Designed By Numina Group
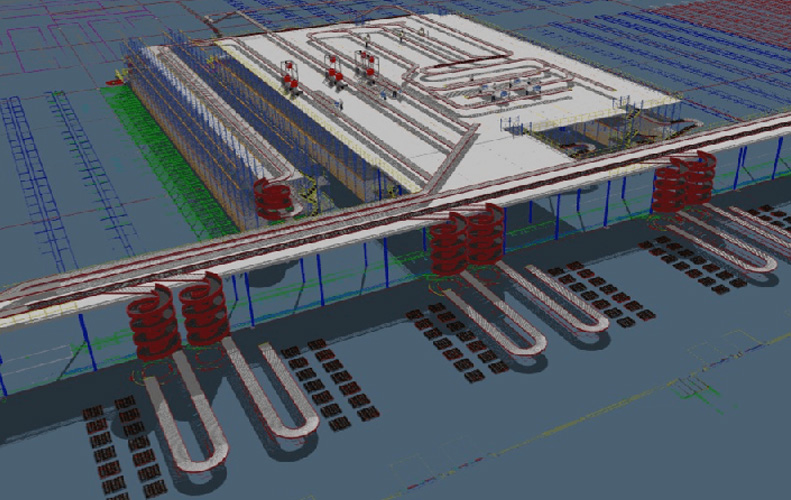
Modern Materials Handling’s cover story describes how The Numina Group helped a client implement automated conveyer systems for omni channel distribution…
Numina Group earns Top TGW Conveyor System Supplier Award
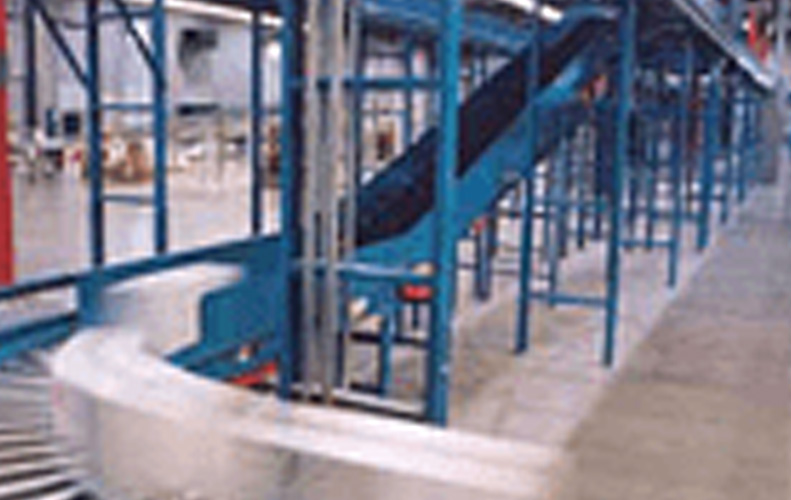
TGW will present Numina Group with the Platinum Award at Modex 2014 at a Press Conference in Numina’s Booth 4723 on March 18th at 3:30 pm…
Latest Pack Automation Technology for E-Commerce Order Fulfillment
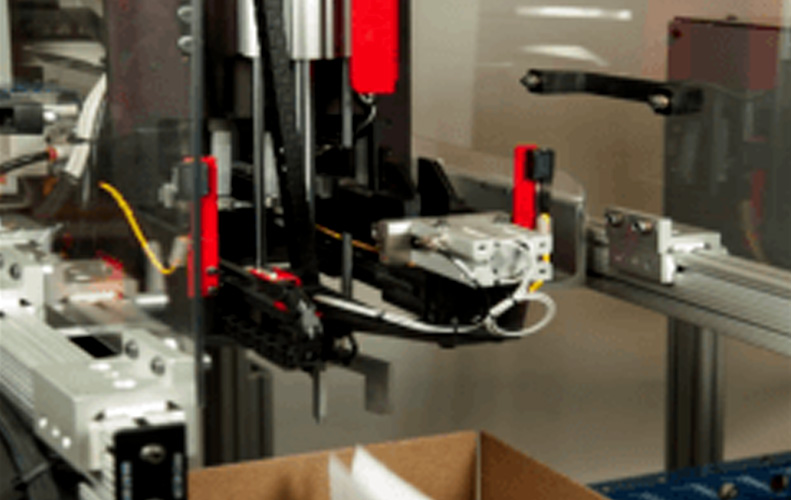
LitPack™ Print-Fold-Insert (PFI) of Pack Sheets and Invoice Documents automates the insertion of order specific documents and promotional materials…
Voice Picking Demos Innovation at IRCE 2013
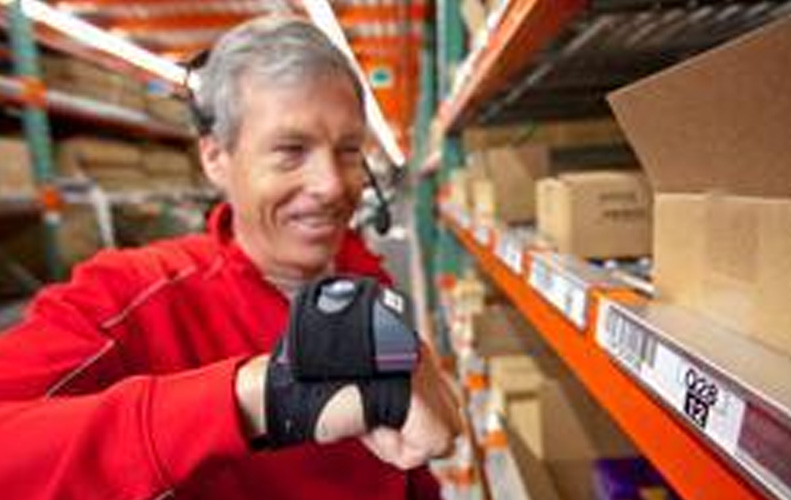
Omni-Channel and E-Commerce Order Fulfillment Automation Expert, Numina Group will demonstrate their latest innovations
The Numina Group earns Prestigious TGW Award
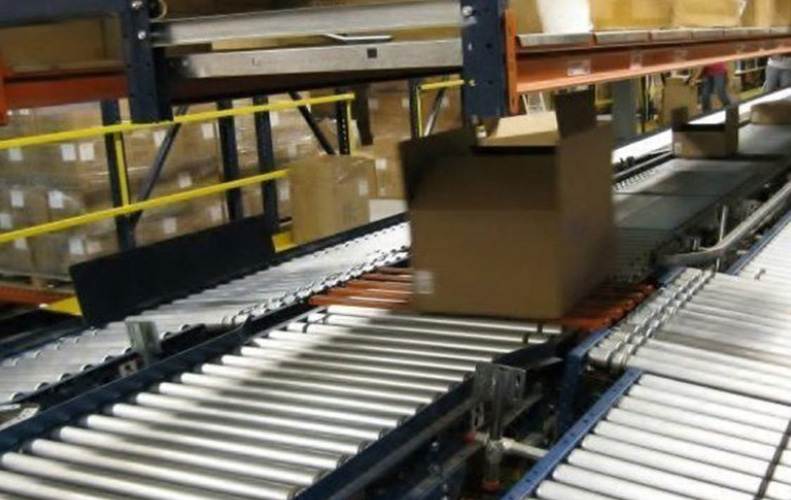
Numina Group has been awarded the prestigious TGW sales award for the second consecutive year. Numina Group, a leading supplier of automated order