Visit Numina Group in Booth #B3519 at MODEX 2018
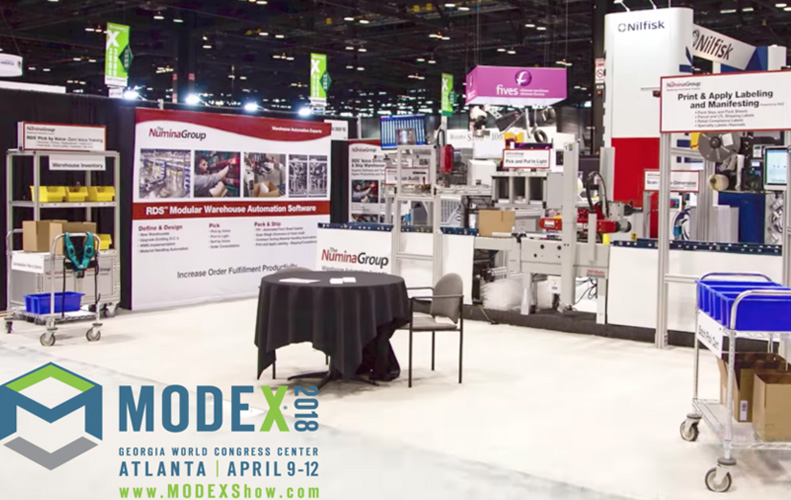
Stop by Booth #S3452 and learn why intuitive pick-by-voice, put-to-light order consolidation, and pack-and-ship automation have provided our customers documented savings of 50-70% workforce productivity gains!
I TECHNICIAN SPOTLIGHT I
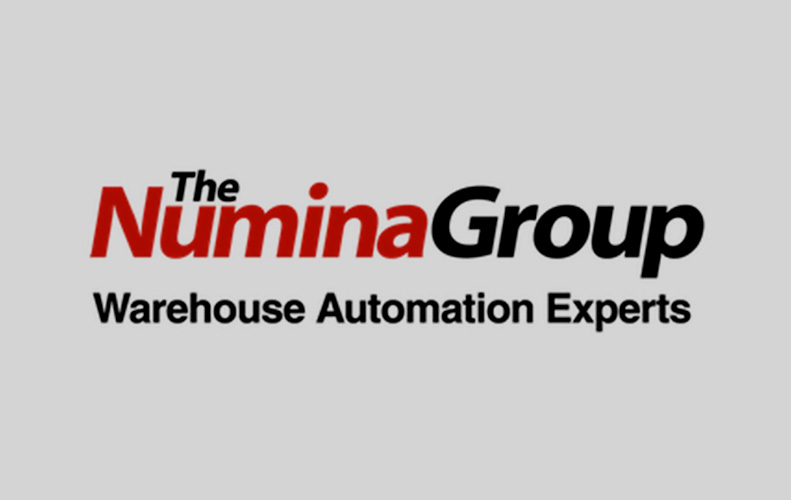
Numina Group’s dedicated service manager, Eric Raschke, was recently featured in Materials Handling MRO Magazine. Read more about Eric here.
Pack to Light Featured at ProMat 2017
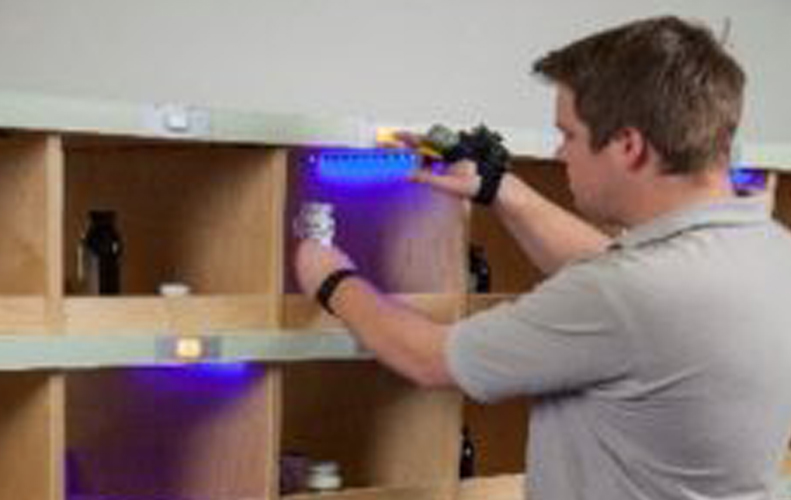
Numina Group will demonstrate their RDS, their Real-TIme Warehouse Execution (WES-WCS), which combines pick-by-voice and put-to-light order picking and consolidation into a pick, pack, and ship suite for e-commerce and omni-channel distribution operations.
Webcam Vision Capture
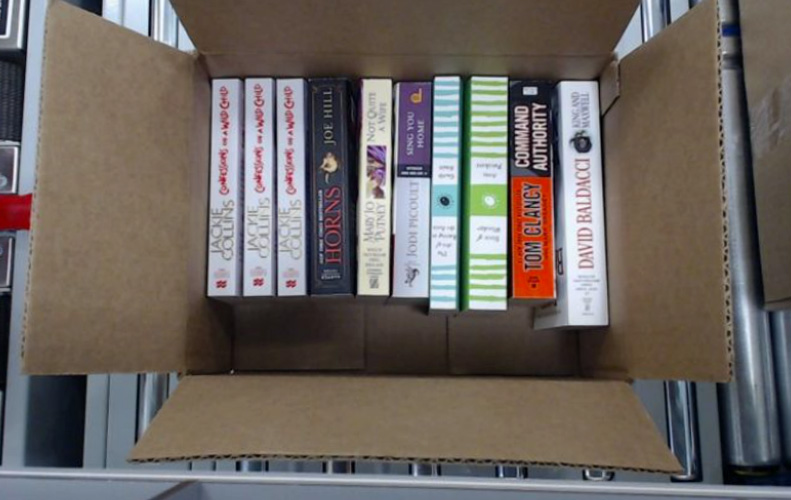
Numina Group has submitted the next-generation vision capture technology for accurate shipping for the Promat 2017 Innovation Award.
Numina Group Announces the Release of a Full Featured Warehouse Management System, WMS
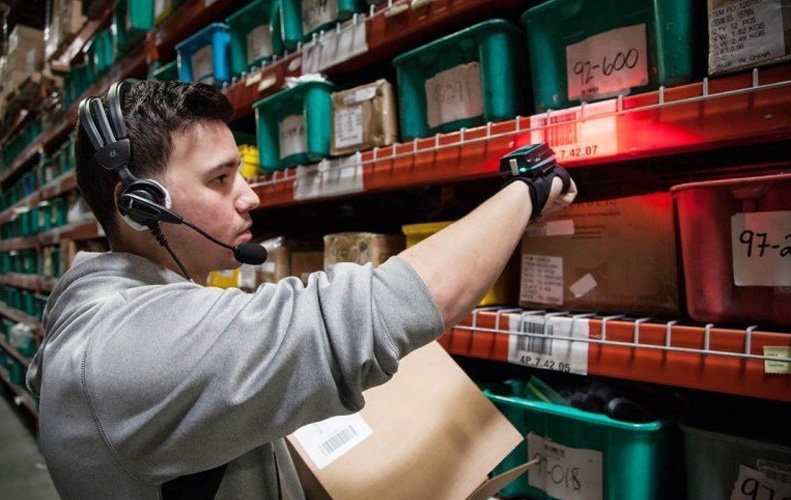
WOODRIDGE, IL – Provider of warehouse and distribution order fulfillment automation, design and engineering services…
Warehouse Voice Picking Success Story
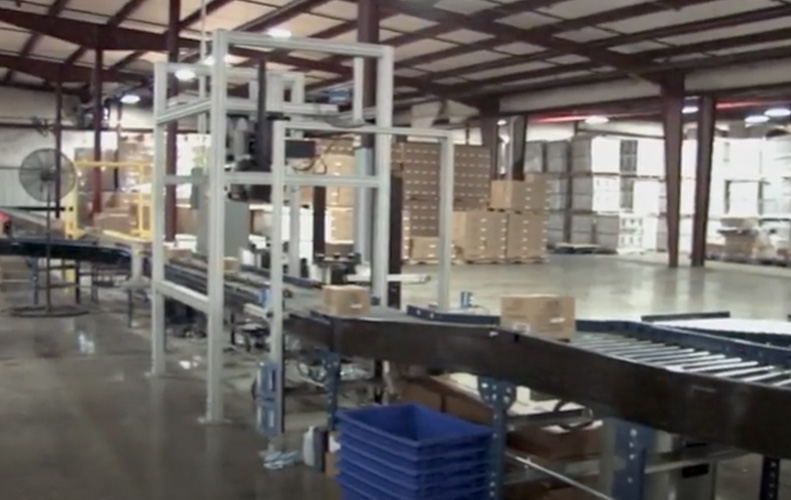
Schumacher Triples Throughput in Existing DCs, Gains a Scalable Solution for Continued Growth With the Numina Group’s Help…
Numina Group Releases RDS Web2™ Web-based Dashboard Interface for RDS™ Warehouse Control and Execution System
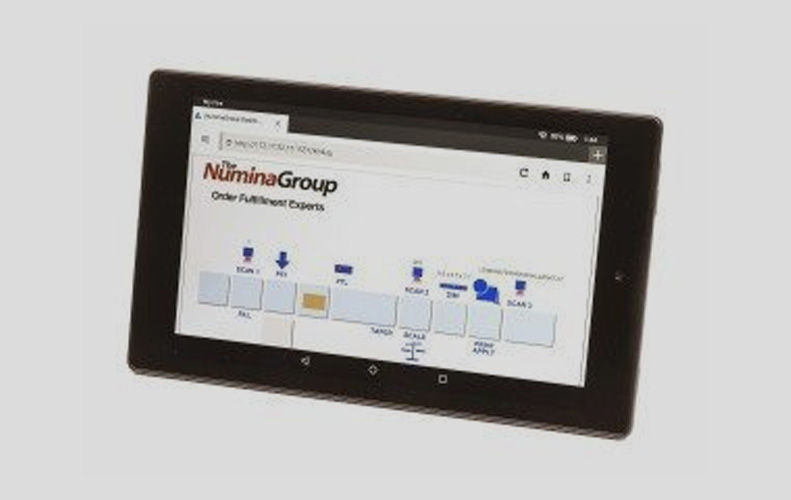
Numina Group announces the release of its latest web based user interface for RDS™, its top tier WES-WCS warehouse automation software platform.
Vision Pack and Audit System, V-PAS™ adds 3-D Camera Technology to Determine the Carton Content, Minimize Shipping Costs, and Improve Customer Service
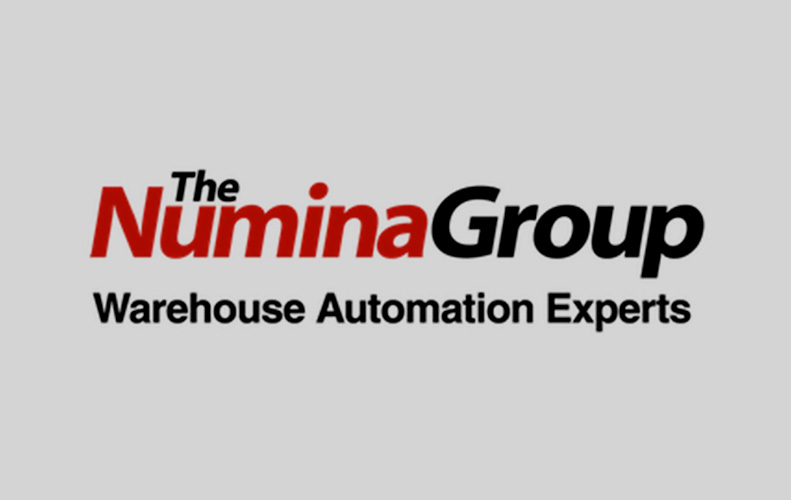
Verifies Pick to Carton has Right Products in Right Size Carton Numina Group announces the release of IFM’s 3-D Smart Sensor Camera incorporated…
Numina Group to demonstrate order fulfillment automation technologies at MODEX 2016 Booth 4427
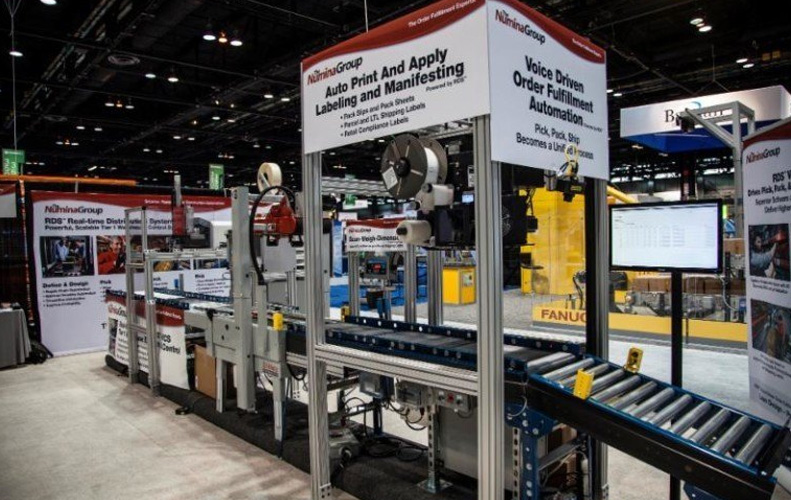
Numina Group, a leading supplier of Warehouse Execution and Control Systems, WES-WCS and material handling integrator, offers over 30 years of experience…
Numina Group named “2015 Integrator of the Year” by Panther Industries
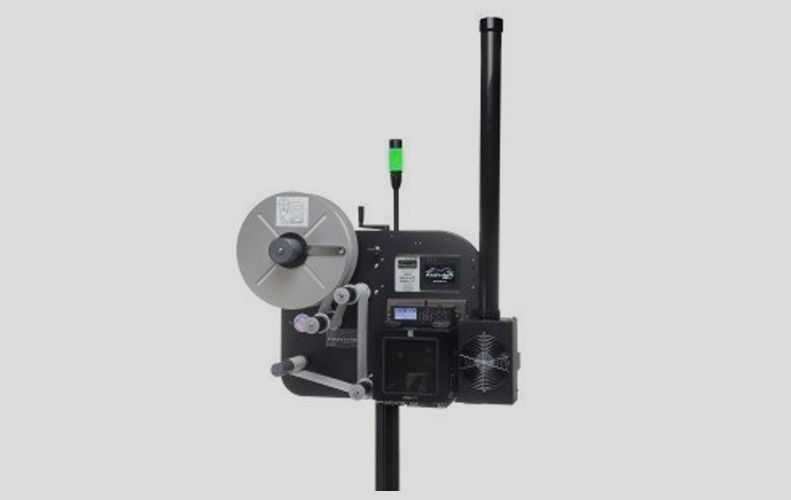
Woodridge, Illinois, February 10, 2016 Numina Group, a leading supplier of automated warehouse control systems, has been awarded…