Save Money with Advanced Cartonization Software
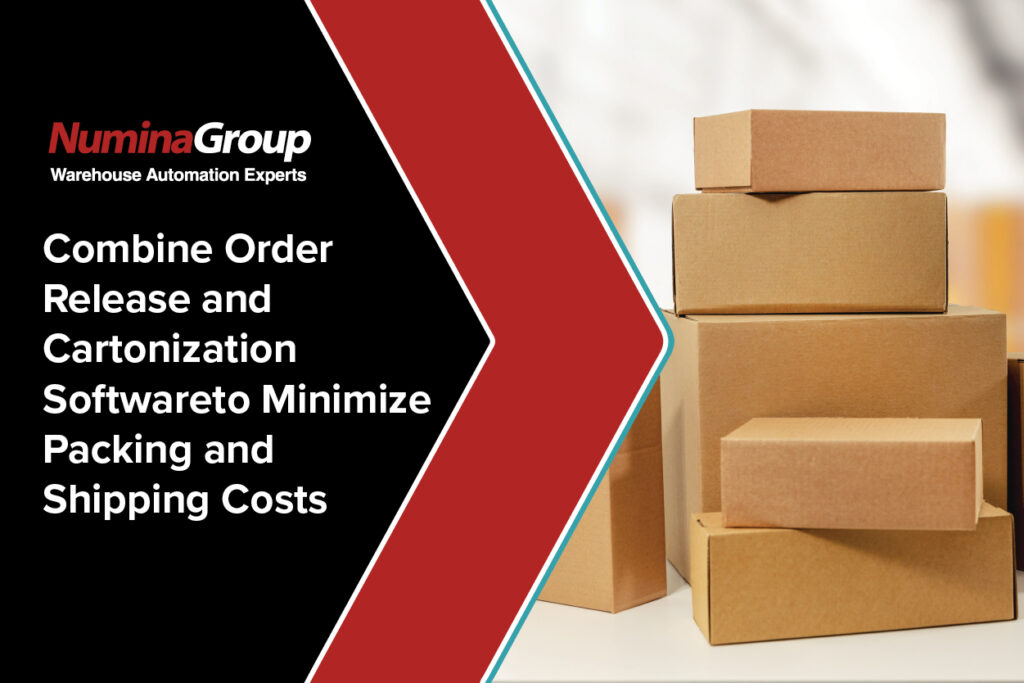
Relying on employees to choose shipping cartons for every order is time-consuming, costly, error-prone. Save time and reduce labor & shipping costs with cartonization software.
Stop Manually Packing and Shipping – Discover Pakt™
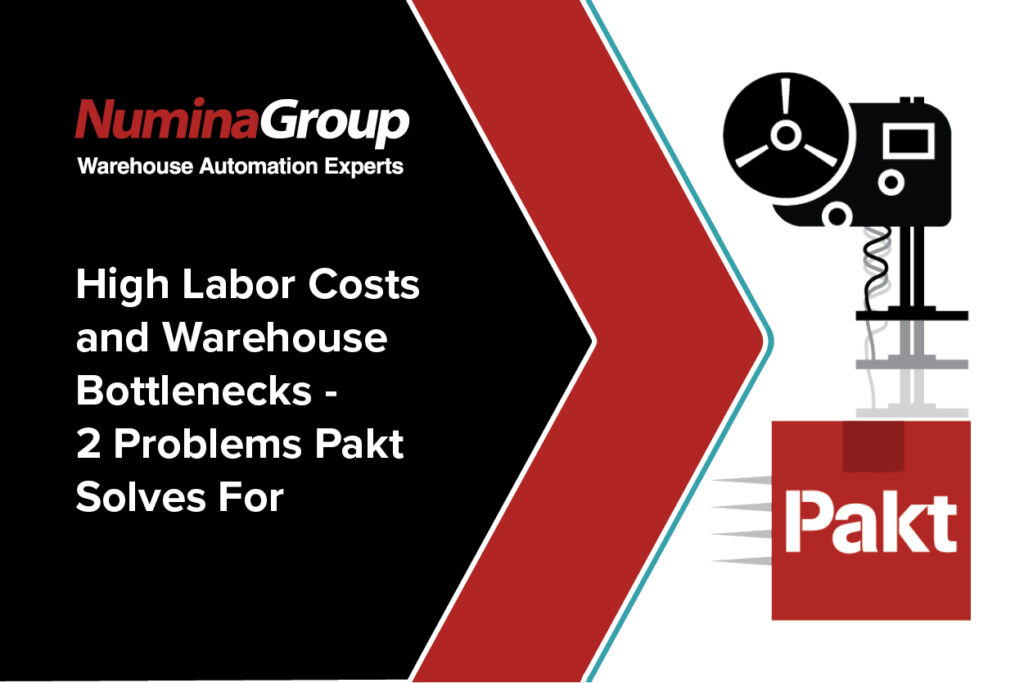
Learn about Numina’s newest warehouse automation solution, Pakt™, a fully productized pack and ship automation solution that is purpose-built for fulfillment operations.
Where are the Case-Picking Autonomous Mobile Robots?
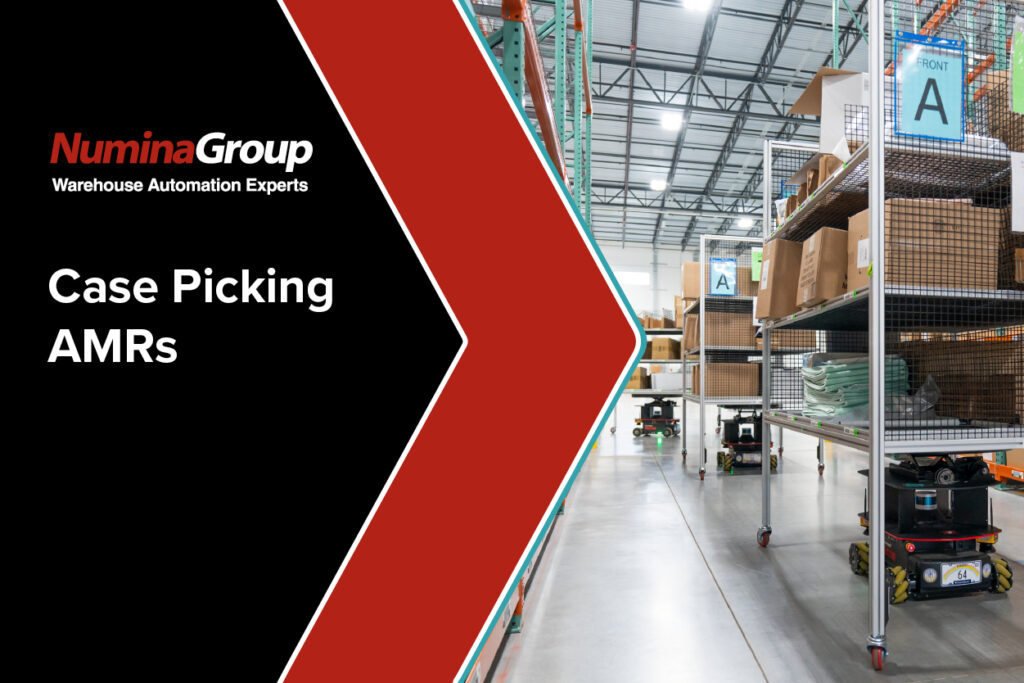
Learn more about our case-picking robotic solution, BatchBot, the latest addition to our family of warehouse automation solutions.
What is Slotting in a Warehouse? Benefits & Tips for Optimization
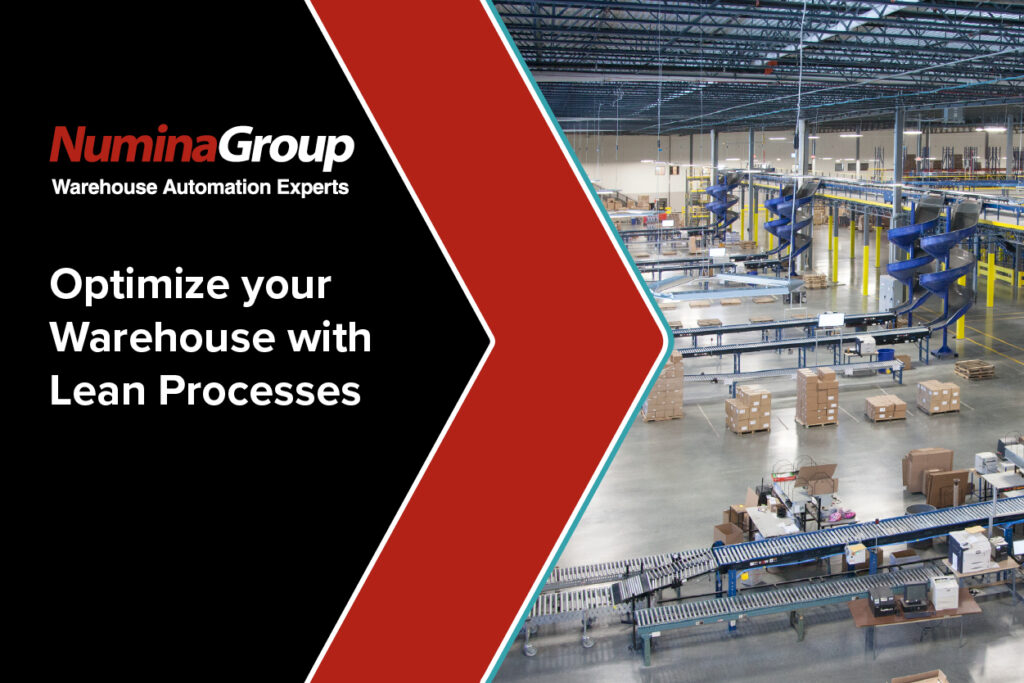
A intelligent slotting system will increase productivity and reduce labor hours to move, store, replenish, and fulfill your orders on a timely basis.
The ROI of Voice Picking
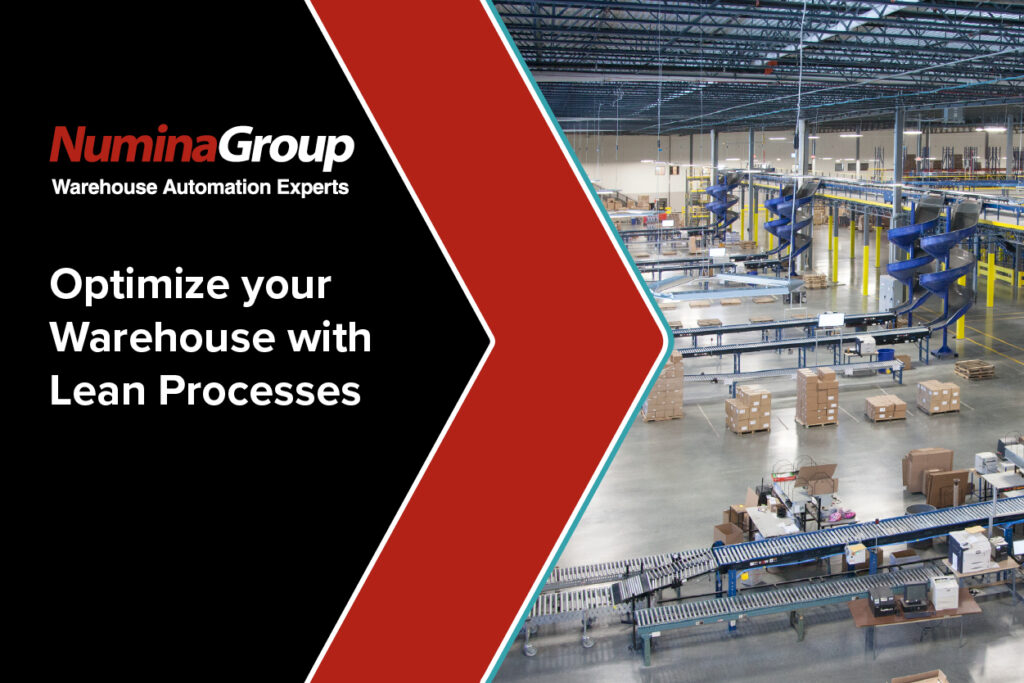
How to quantify the cost-saving benefits of voice picking technology, a proven method to reduce manual picking tasks, lower labor costs, and increase profitability.
The Basics of Warehouse Automation
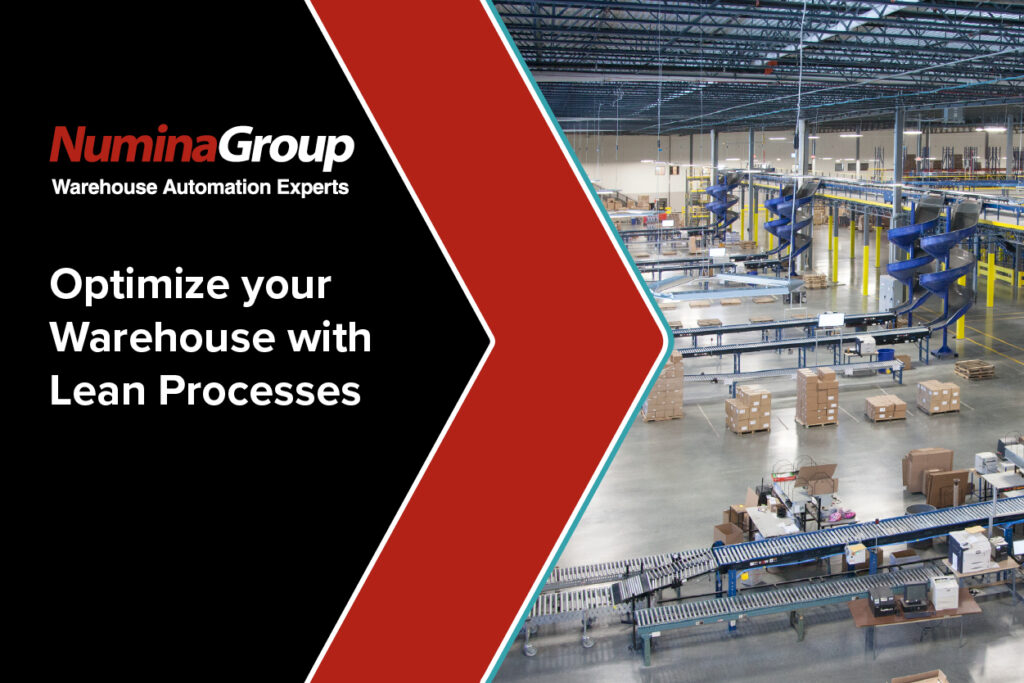
The goal of warehouse optimization is to increase efficiency and profitability by deploying lean processes. Here’s how to achieve these benefits through best practices & the right blend of warehouse automation.
Order Picking Automation Options to Resolve Warehouse Labor Shortage Challenges
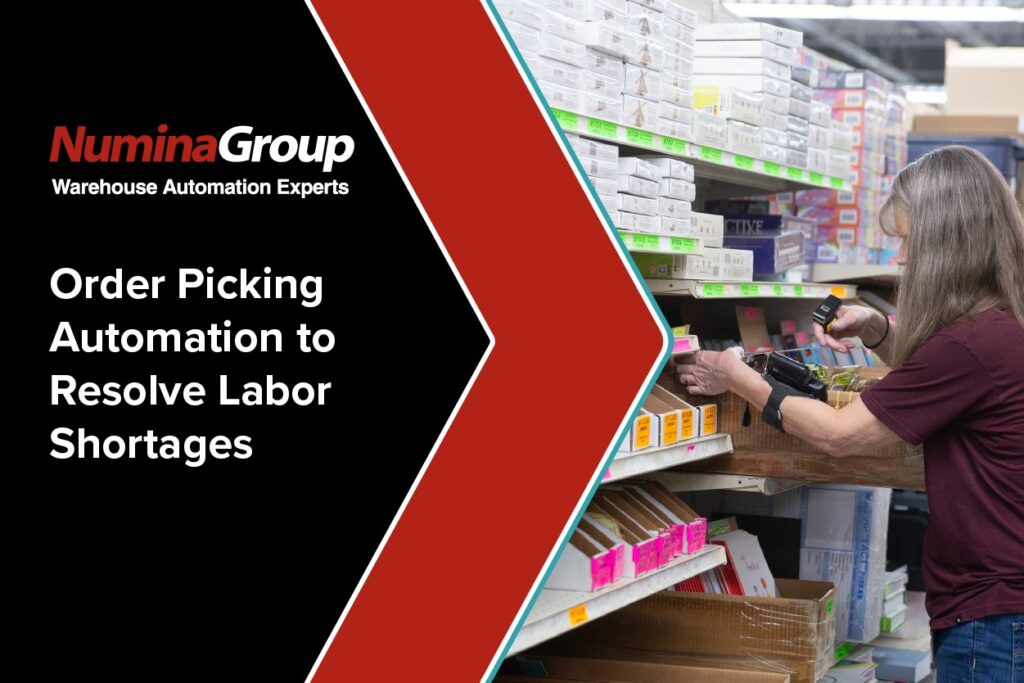
Today’s shippers have many options to consider to automate order fulfillment in warehouse operations. Here are factors to consider.
Seven Steps to Prepare for the New World of Peak Season Shipping
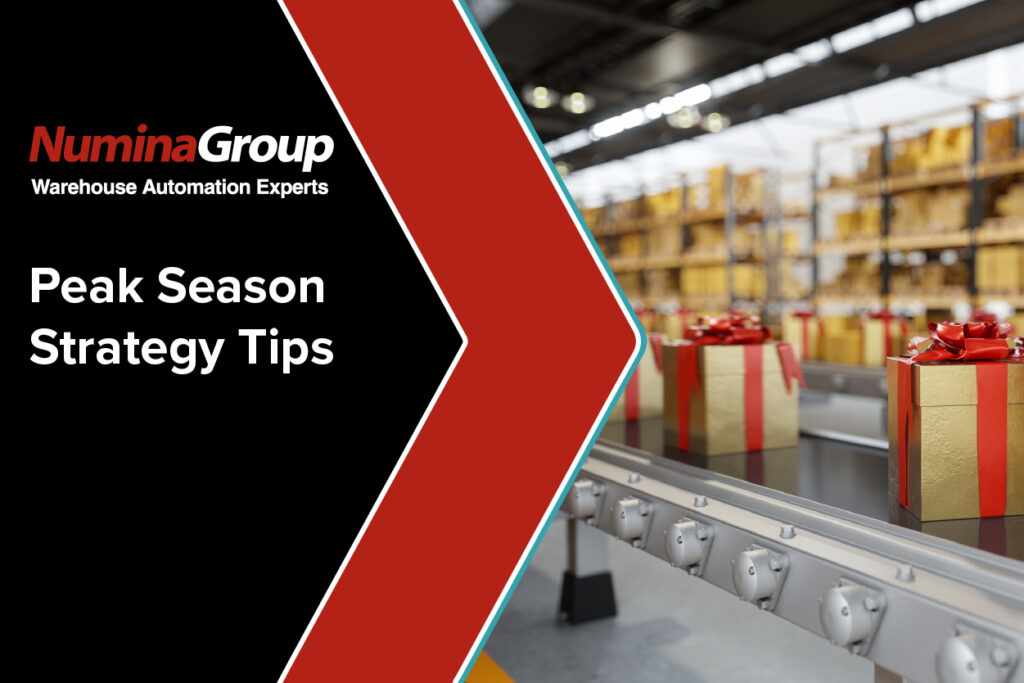
Unpredictable customer demand is resulting in not one, but many peak seasons for retailers. Key steps your company can take now to to stay ahead.
Improve Picking Productivity and Reduce Labor Costs with Victory Voice Picking Technology
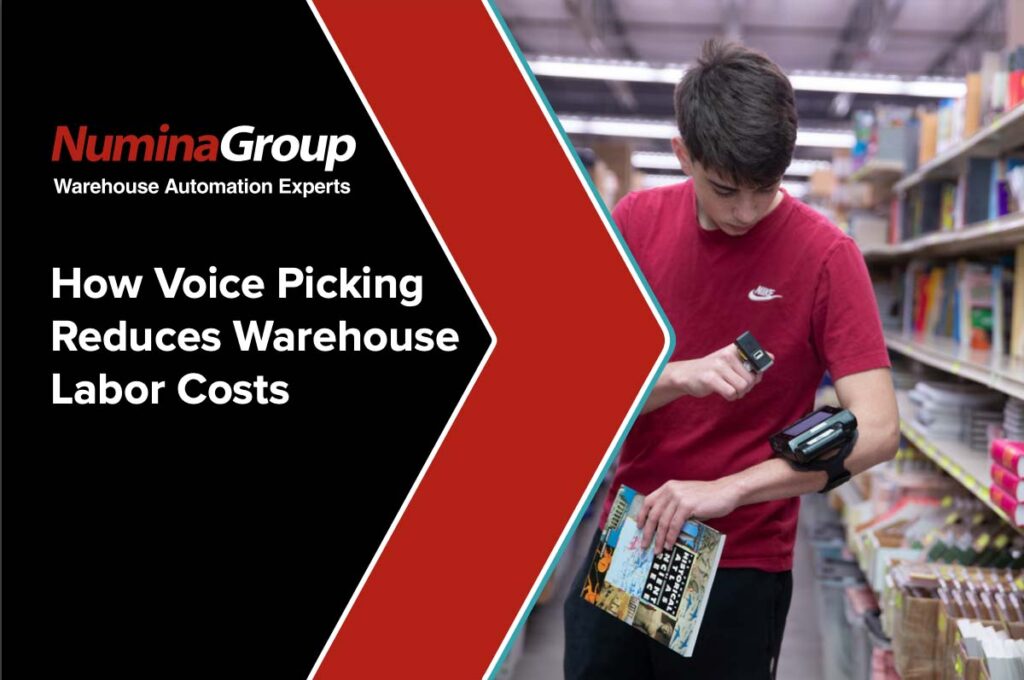
Pick-by-voice technology is a proven method to reduce manual picking labor, and a high-priority warehouse improvement a company can make to increase business profitability. Learn why.
Cost and Performance Benefits Offered by the Latest G2P Warehouse Robot Solutions
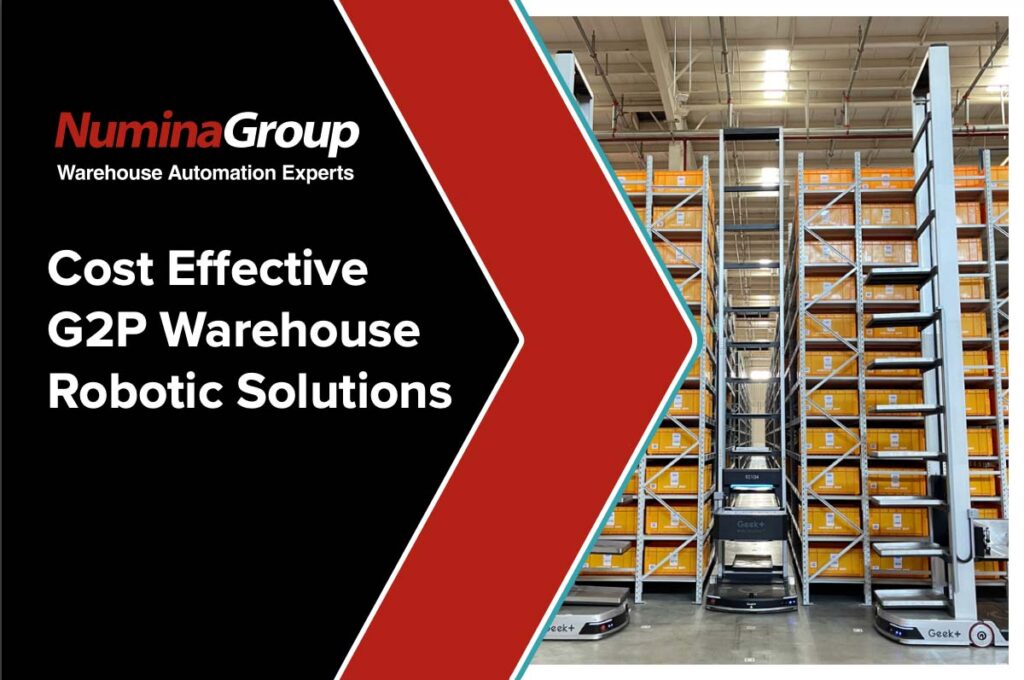
Innovations in warehouse robotic solutions are yielding higher efficiency and flexibility in order fulfillment, while reducing the investment cost of goods-to-person (G2P) solutions for mid-sized to large distribution operations. Learn why.