How is Pakt Different from Legacy Pack and Ship Solutions?
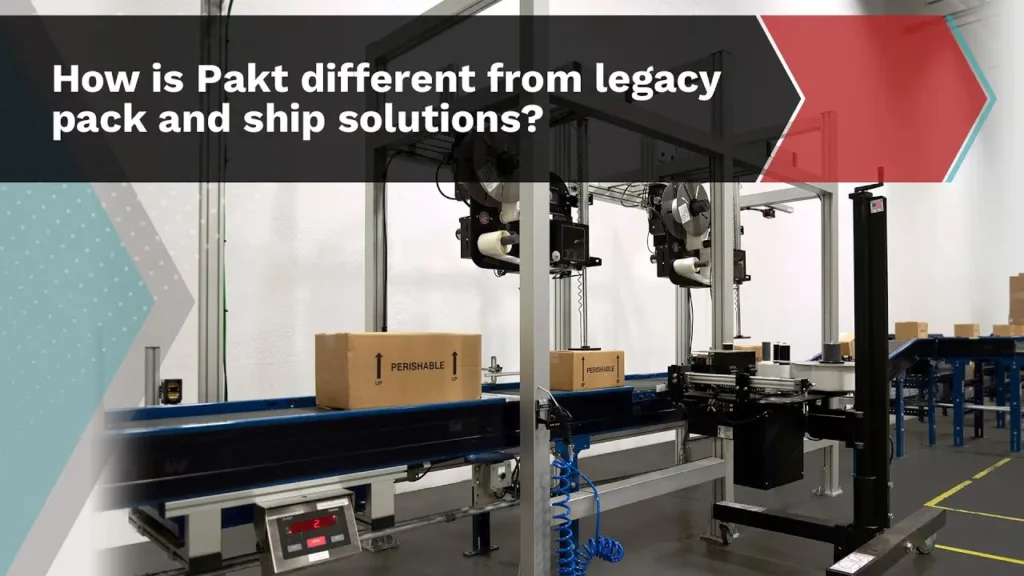
What are the Components of Pakt?
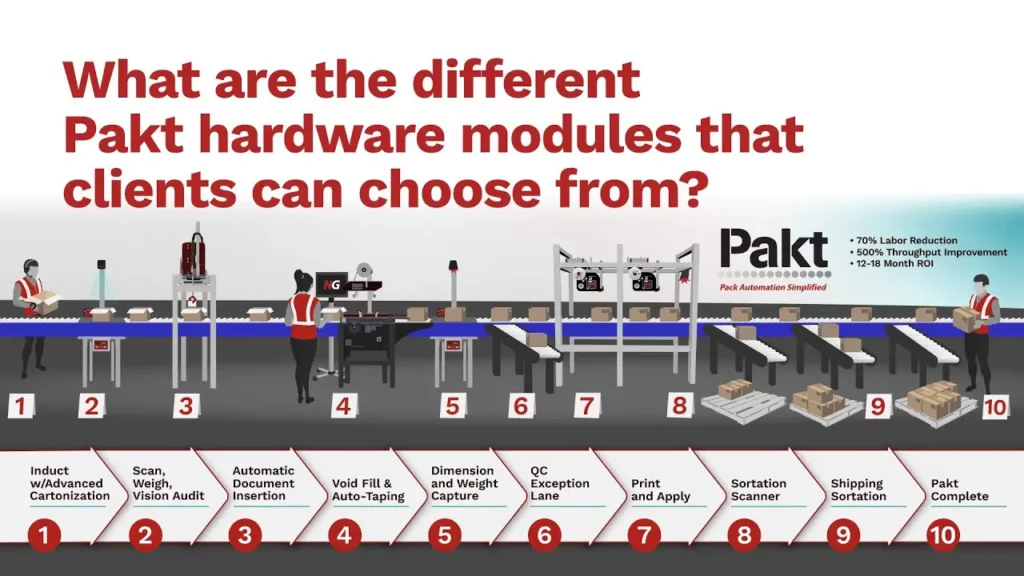
Leveraging Pick Modules to Accommodate Higher Order Volume
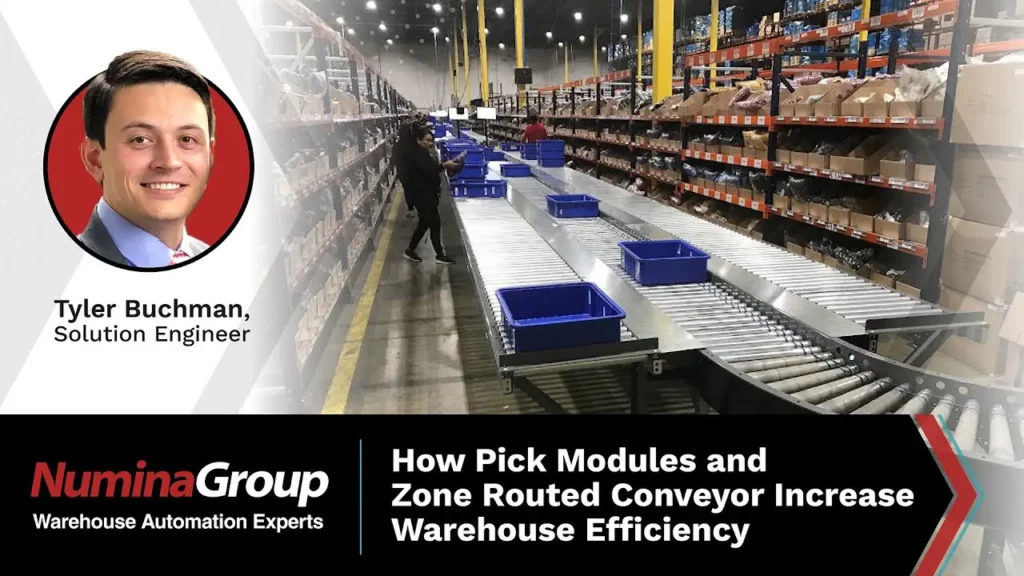
Zone routing conveyor systems are commonly used in conjunction with pick modules in warehousing to enhance order picking efficiency. This system is designed to automate the movement of products through the different zones or pick modules within a warehouse. Within each zone, a conveyor system is installed to transport items between different locations or zone […]
RDS Victory Voice | Multi-level pick modules
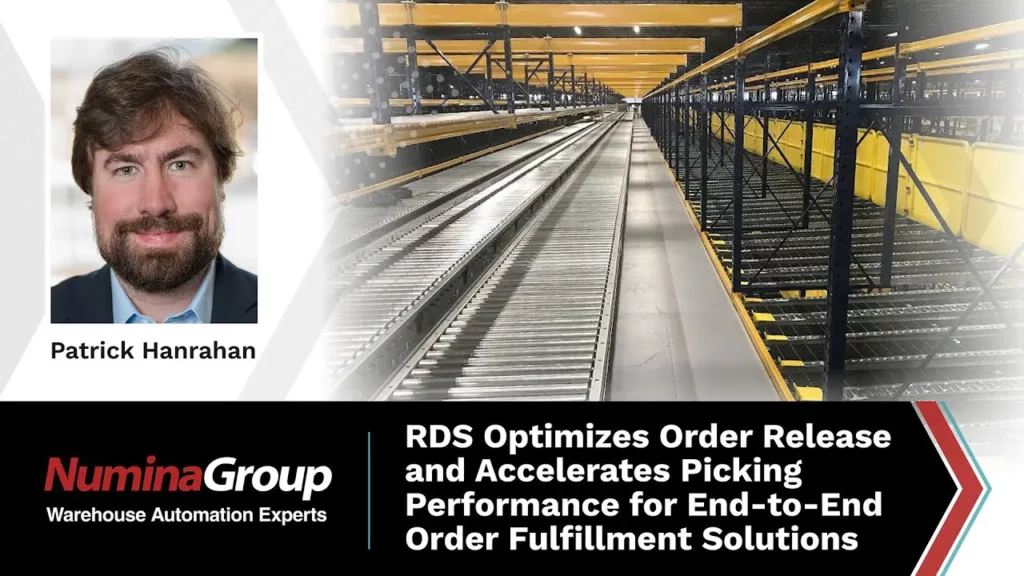
Warehouse automation drives down operating costs to lower the labor per order fulfilled. The challenge is determining which blend of automation technologies best suits your business requirements with the highest impact on reducing manual labor. At Numina Group, we design customer solutions combining leaner processes, better operation practices managed by the right software modules, and […]
Warehouse Automation Integration Walk Though | Deep Dive
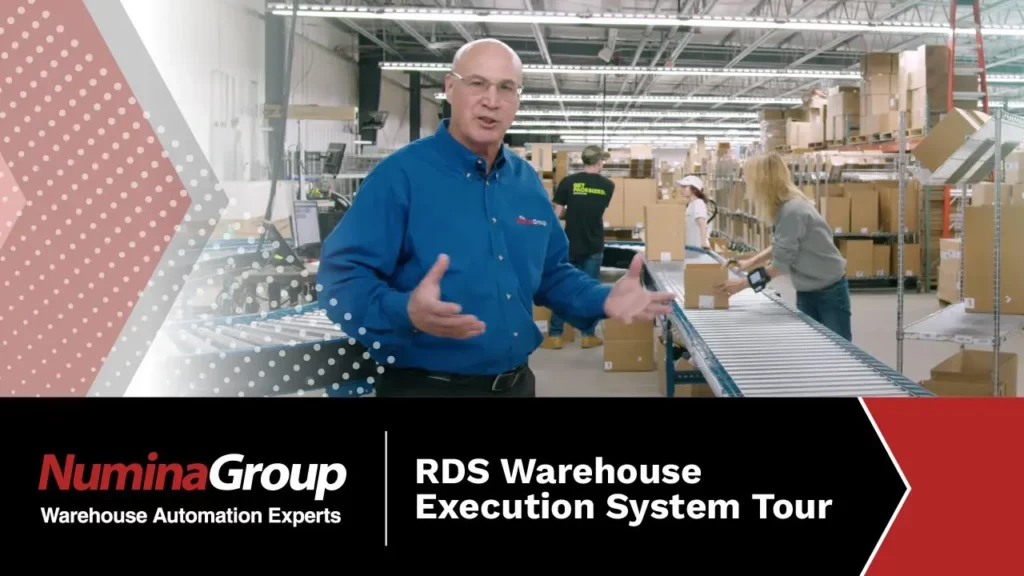
See a live demonstration of automated order fulfillment system, fully managed and synchronized by Numina Group’s RDS warehouse execution software platform. Tim Hanrahan explains how educational supplier Rainbow Resource increased daily order fulfillment throughput by 70%, with less staff, with a Numina-recommended warehouse automation solution tailored to its operations. Rainbow implemented Numina’s RDS™ Real-Time Distribution […]
Goods-to-Person and Autonomous Mobile Robot (AMR) Solutions
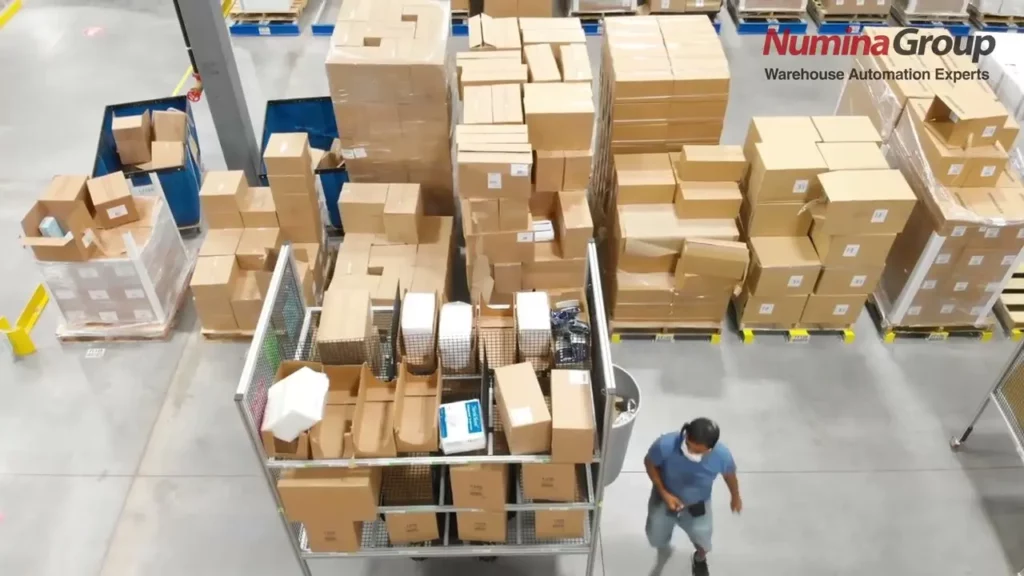
Advancements in the latest generation of robotic-based goods-to-person (G2P) and autonomous mobile robot (AMR) technologies have lowered the cost and made the technology suitable for all sizes of warehouse order fulfillment operations. The latest generation of robotic G2P and AMRs are cost-effective and scalable solutions, especially if the order profile consists of a large percentage […]
Pakt – Post-Pick End-of-Line Pack and Ship Automation
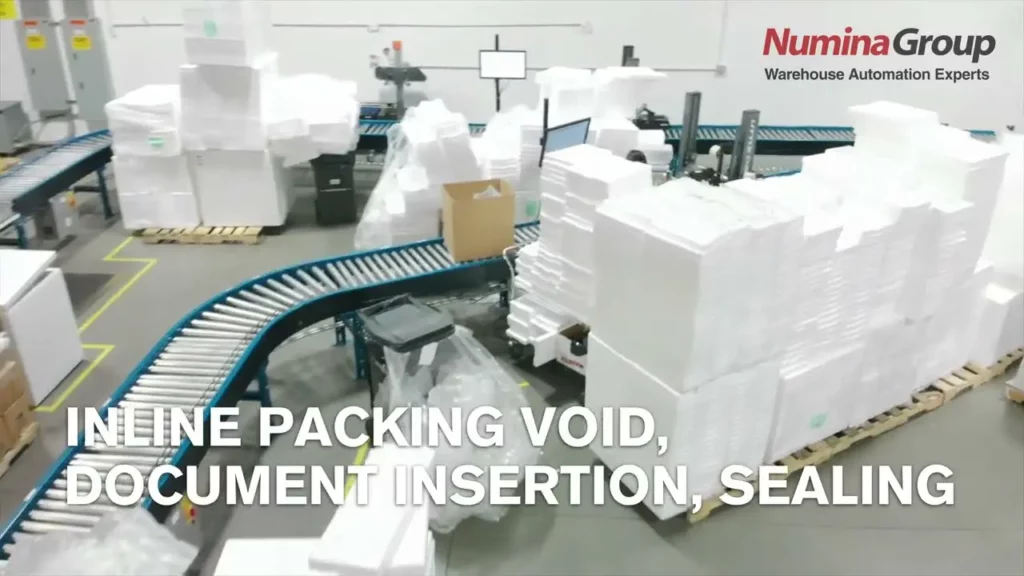
Print Fold Insert (PFI) | Automated Document Print and Insertion System
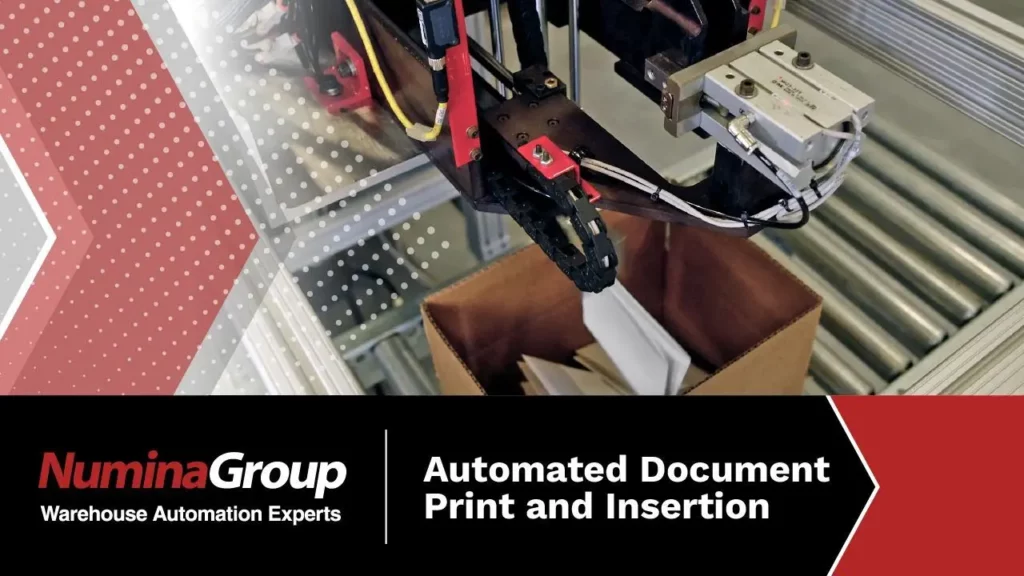
Reduce warehouse labor costs by automating document generation and insertion on shipping orders with Numina’s Print-Fold-Insert (PFI) solution. PFI performs automated document print-on-demand and precision placement of documents into an open carton or tote. PFI automatically prints, stacks, folds, and inserts up to ten 8.5″ x 11″ packing sheet documents into a shipping carton or […]
One-Step Print and Apply |Pack Slip Under Ship Label
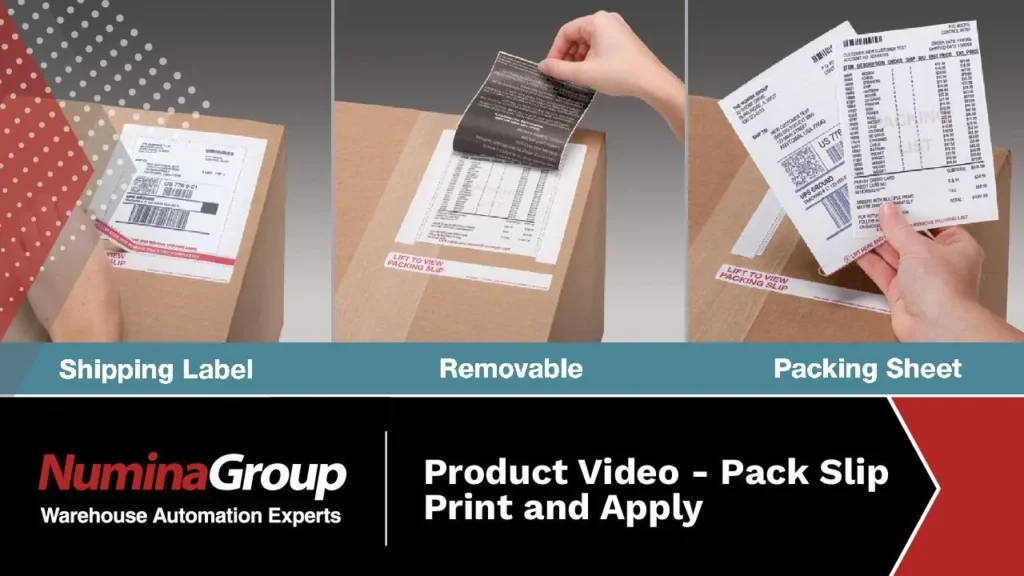
Boost fulfillment productivity with Numina’s fast automated application of a 4″ X 6″ packing slip underneath a shipping label. This short video shows efficient automated printing and application of the pack slip in a seamless workflow with minimal worker touches using Numina Group’s One-Step™ Fulfillment System. Numina’s One-Step print and apply solution is a next-generation […]
United Medco Reduces Order Fulfillment Costs by 60% with Numina Warehouse Automation
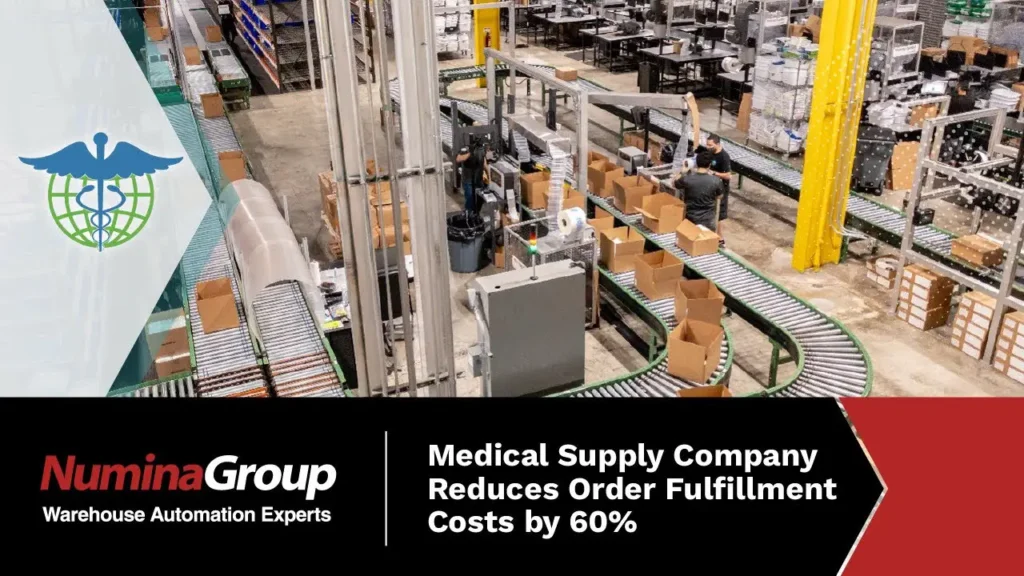
United Medco worked with the Numina Group to audit their operations in a warehouse systems design study that identified process improvements and the best approach to automate its pick, pack and ship operations.