Voice Directed Order Fulfillment Automation for Frozen Food Fulfillment
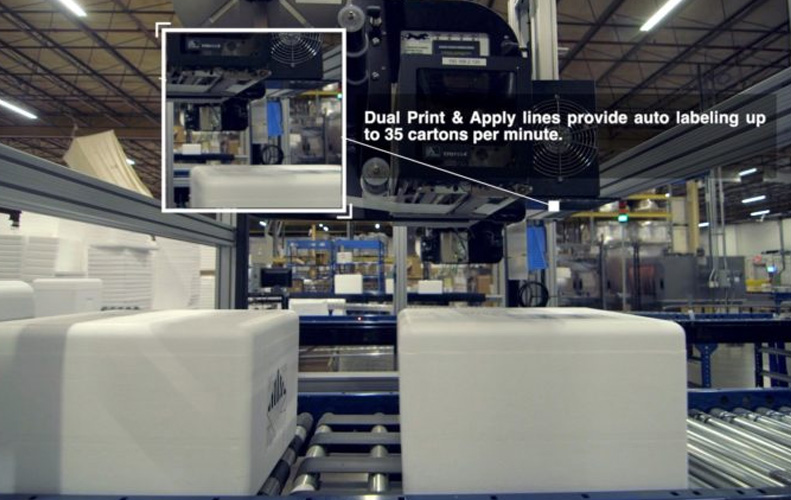
Success Story Founded over 100 years ago, Neesvig’s is privately held meat processing and food fulfillment firm that specializes in temperature controlled and frozen food fulfilment. They distribute products nationwide as a one-stop shop for e-com direct to consumer deliveries. Acting as a third party logistics service provider for dozens of top brand food suppliers and retailers,…
Value Stream Mapping
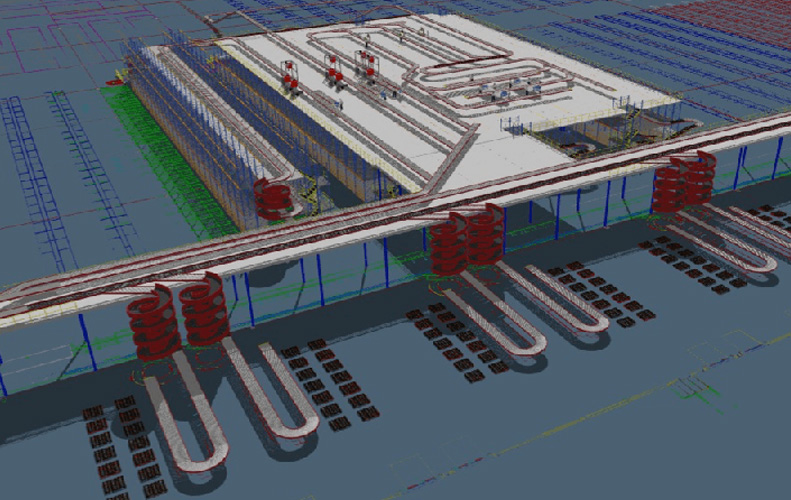
Eliminate Waste in your Order Fulfillment Operation with Value Stream Mapping In an earlier post, we discussed how upfront planning to define the right DC design road map can lead to free warehouse automation thanks to a rapid ROI generating significant cost savings. Studies show that best-in-class companies that emphasize continuous improvement, invest in value…
How Mechatronics Shows the Path to Higher Productivity in Order Fulfillment Automation
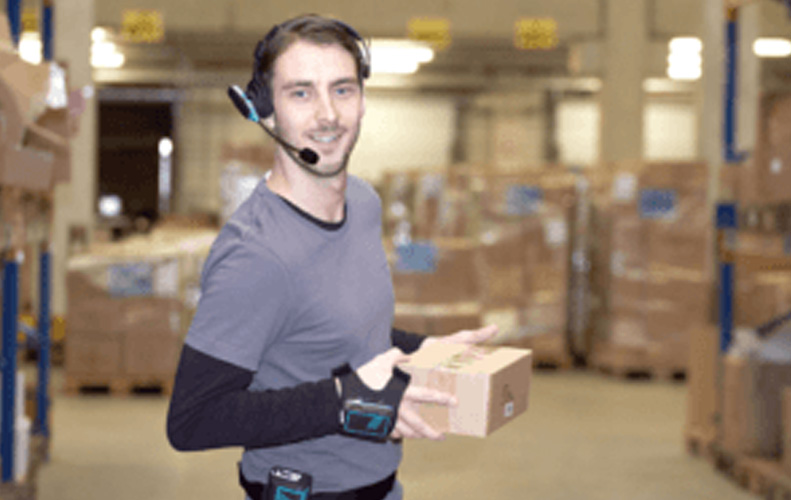
Far too often, distribution operations compartmentalize areas and direct managers to focus on solving daily operational issues and requirements in specific departments within the distribution center (DC). However, a more effective approach is to combine higher accuracy and more efficient design driven with technologies such as pick-to-voice, and then combine better picking with pack
How Warehouse Automation Helps Retain Good Employees
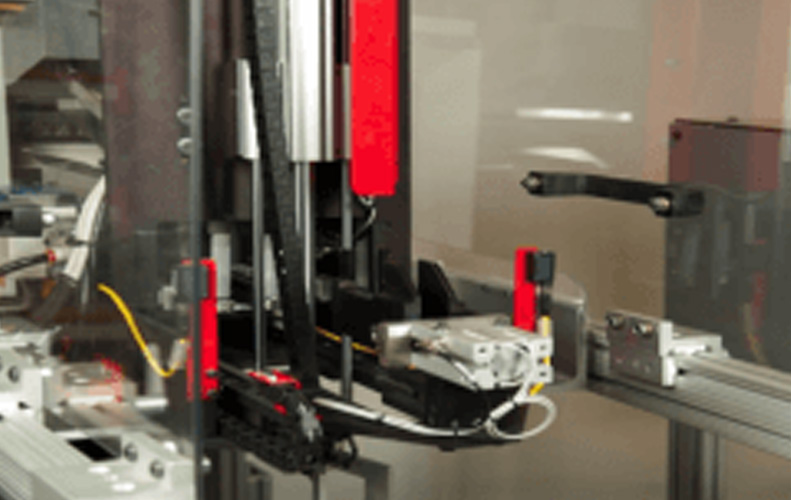
How to Retain Key Warehouse Staff in a Tight Labor Market Crain’s of Chicago recently announced that Amazon will be opening a second distribution center (DC) in Joliet, IL, bringing 2,000 new jobs to the area. In addition to Amazon, Whirlpool, Michelin North America, and IKEA are also opening or planning to open large warehouses…
How the Right DC Roadmap Can Lead to Free Warehouse Automation
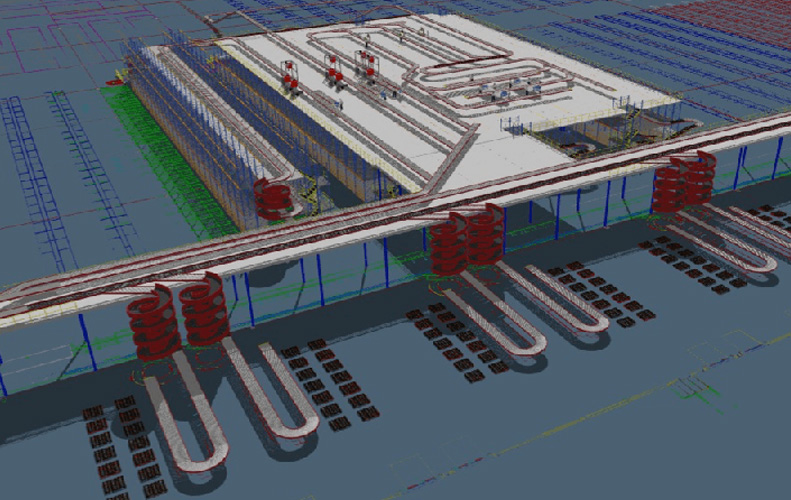
Companies today are grappling with major challenges in their quest to maintain a competitive edge. Trends such as the explosion of e-commerce, lower levels of business on-hand inventory, retailers becoming e-tailers, and the demand for same-day deliveries are all placing tremendous pressure on business operations to keep up. The need for accurate, on-time order fulfillment…
Labor Tracking and Performance Metrics Bundled with Voice-Directed Order Fulfillment Automation
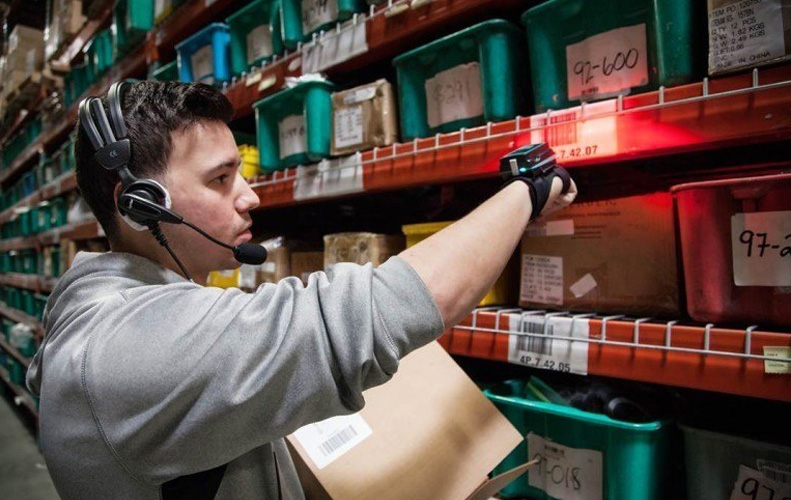
Labor costs account for 50% to 70% of a distribution order fulfillment operation’s operating costs. Increasing worker productivity by 30% or more by implementing voice, especially in picking, can generate a fast return on investment many times in under one year. This is especially true if the investment can provide labor tracking and measure worker…
A Top Tier WCS Increases Productivity in Omni-Channel Distribution
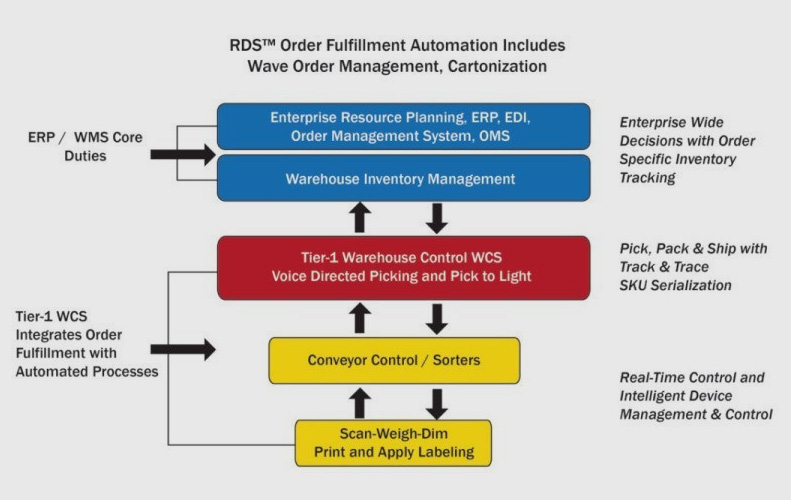
Many times complex order fulfillment automation goes beyond just adding voice to a DC, it requires a software platform to manage order release balancing to optimize the entire pick, pack, and ship order fulfillment operation. This is the domain of a top tier Warehouse Control and Execution System, (WCS) that includes software to balance and…
Why Speaker-Independent Voice is the Right Choice for your DC
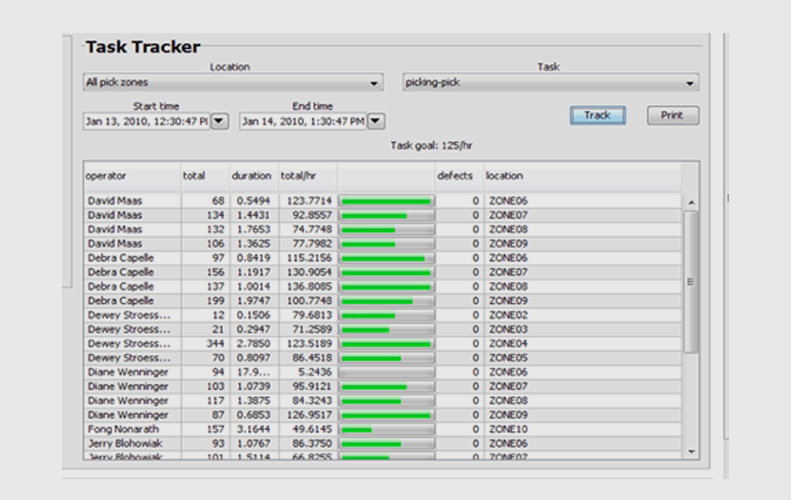
Picking can be the most labor-intensive activity in omni-channel e-commerce order fulfillment operations, especially piece picking operations. Orders requiring rules like a specific package, color, accessory, promotional item, document, or gift wrapping benefit the most from voice technology because it directs and instructs operators on the required shipment and packing rules. Voice is highly flexible…
Finding the Right Tool for Warehouse Control Efficiency in Omnichannel E-commerce Order Fulfillment
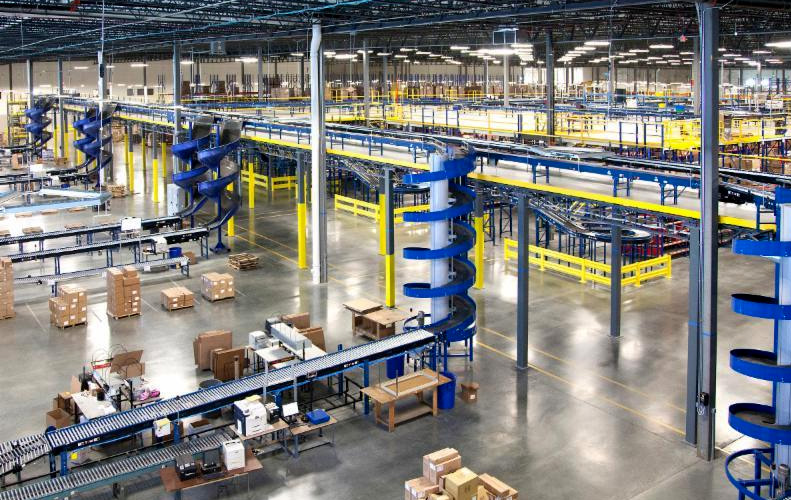
It’s abundantly clear that growth of online retail is impacting every company, regardless of size and industry. Virtually every company requires an e-commerce order fulfillment strategy within their distribution operation. Many operations are struggling to blend split case, low SKU count orders into a more traditional predominately full case, full pallet LTL order profile operation;…
The Latest Trends in Track and Trace SKU Serialization Capture
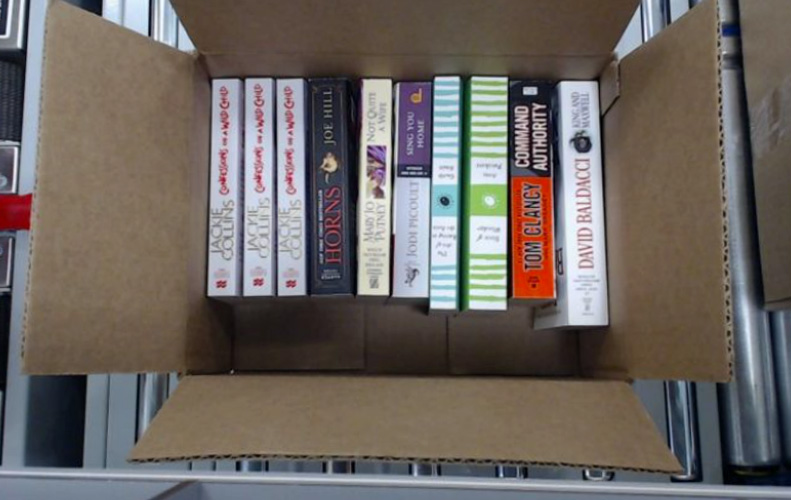
The need to track lot and serial SKU information for order shipment records is no longer limited to specific industries. It exists throughout the supply chain and if it’s not required today in your business it could be coming shortly! Consider the demands of electronics and computer distribution channels, where a warranty begins the moment…