Six Key Features of a Top-Tier WES-WCS
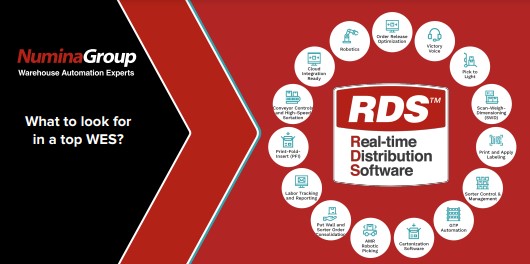
To automate complex order fulfillment operations, it takes a top-tier WES-WCS platform with specific functionality and integration capabilities. Here is what to look for.
Pack & Ship Automation – Moving From Customization to Configuration
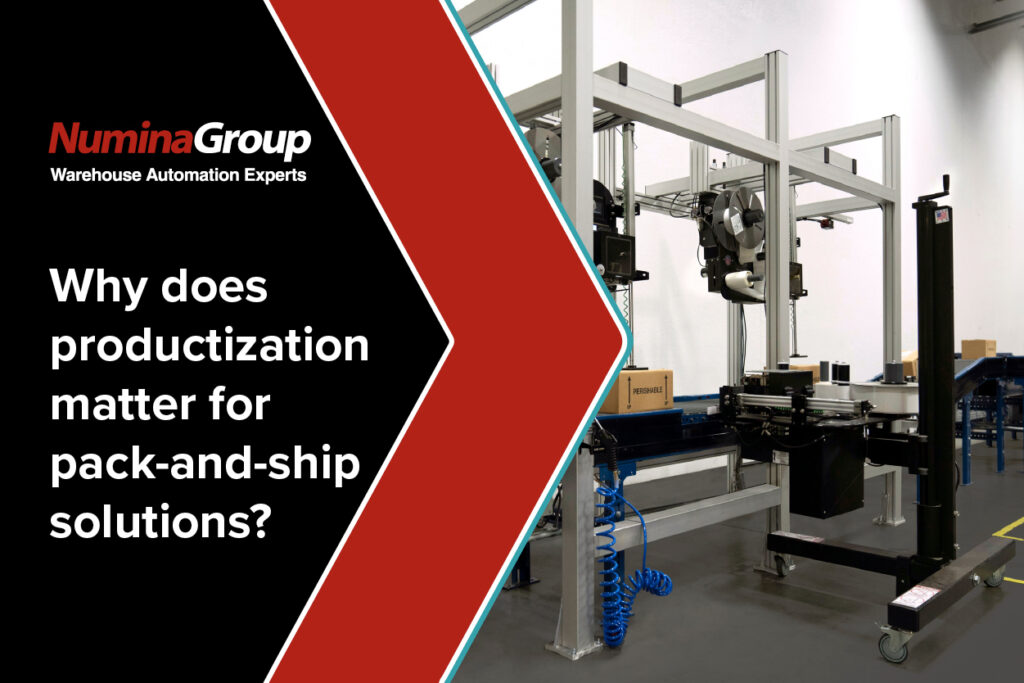
Why does productization matter for pack-and-ship solutions? Learn more about the financial, operational and technical benefits you’ll gain.
Automate an Existing DC or Open a New Satellite Warehouse?
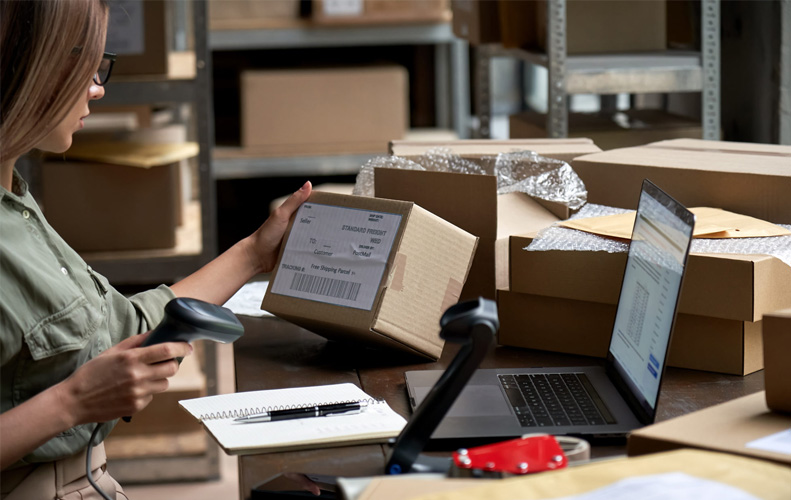
Improve existing operations or add a new facility? There is no one best answer, but asking the right questions will yield the best solution for your business. Learn more.
Voice Picking System Benefits
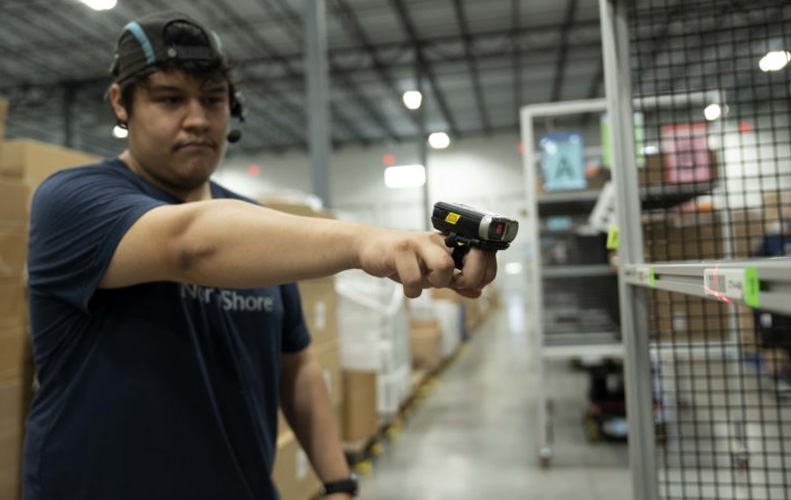
Why a Voice Picking System is the Choice to Accelerate Order Fulfillment. One of the most effective ways to streamline warehouse labor requirements – by as much as 50% – is to add a voice-directed picking system to your picking operations.
How the Right Warehouse Automation Decisions Can Solve Your Labor Woes
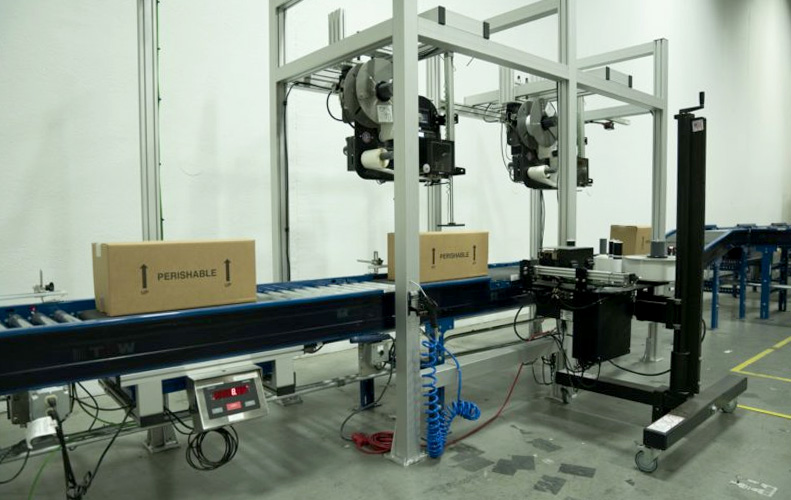
As the economy roars back to life, manufacturing, distribution & warehousing operations face challenges in attracting and retaining qualified workers. The temporary labor pool, which many companies rely on during peak periods, is also shrinking. Warehouse automation can help.
Synchronize people and AMRs
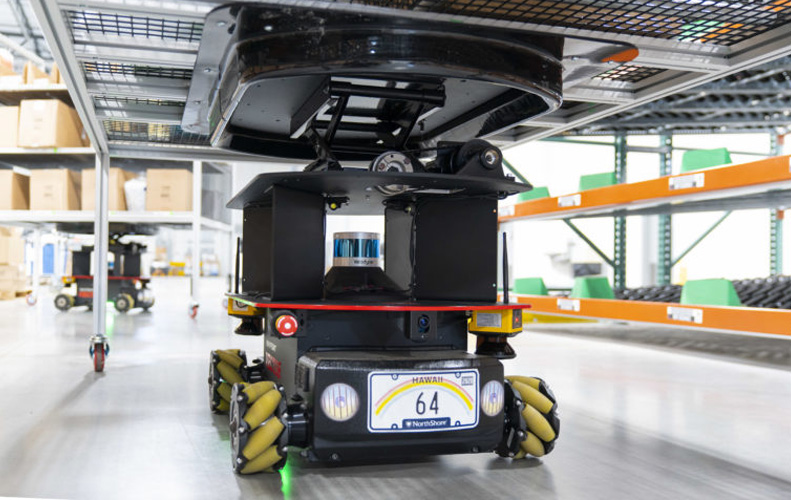
Learn about Numina Group’s “Direct Me,” solution, an innovative warehouse software application that fully synchronizes people and autonomous mobile robots (AMR)s for more efficient picking, packing and shipping.
Prepare Now for Next Peak Season
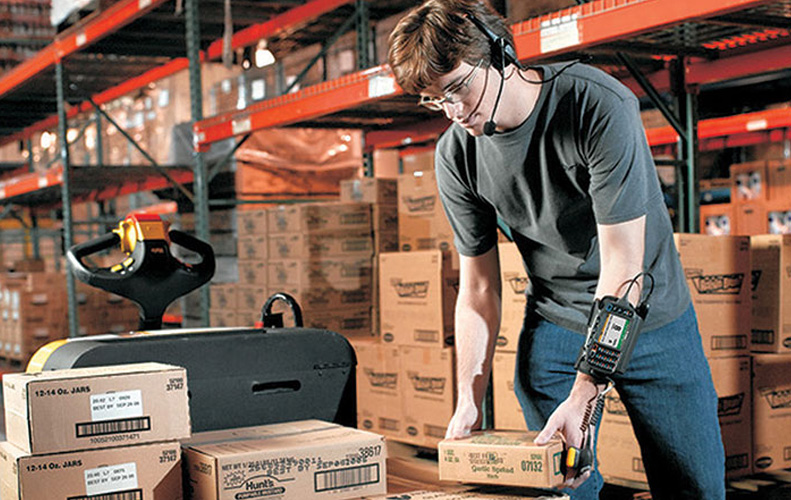
Final numbers aren’t in, but 2020 was a record-setting year for shipments. Unfortunately, over 2 million packages did not arrive on time for Christmas, according to the Atlanta Journal. Although peak season brings in a welcome surplus in profits, it also highlights…
Vaccine Rollout Logistics
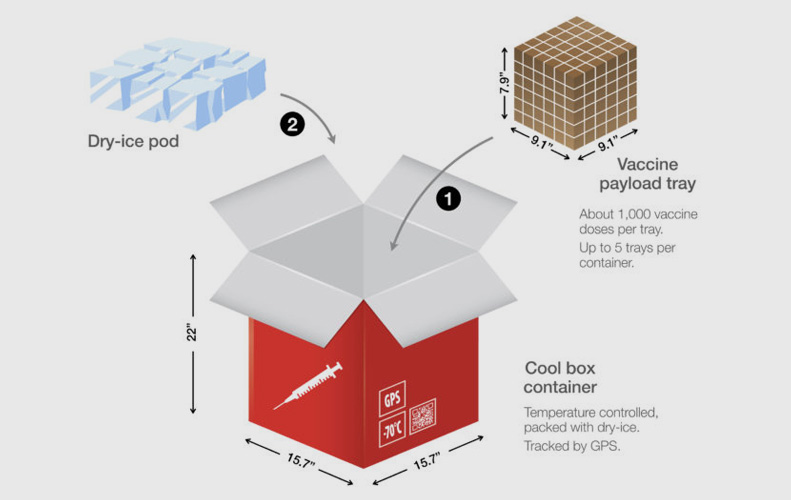
The Logistics Behind Rolling out the Covid Vaccine The Covid 19 vaccine distribution effort is being described as the biggest logistics challenge since World War II
Order Consolidation Put to Light Walls
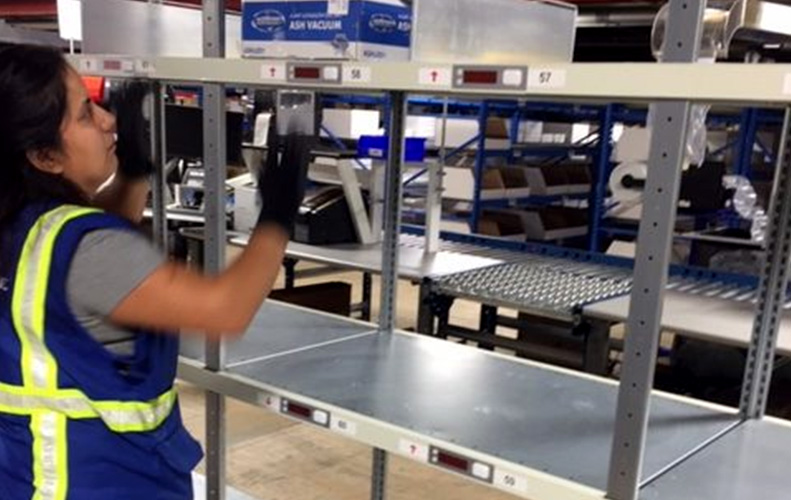
Are you looking for new ways to accelerate and increase order fulfillment throughput without increasing labor costs? Put Walls offer proven benefits. Learn more.
Voice Picking Technology Myths – Debunked
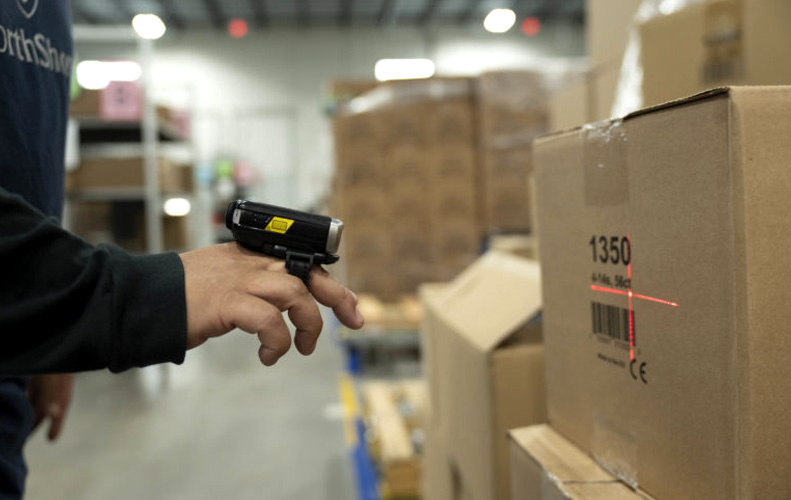
There are quite a few outdated concerns and myths surrounding voice directed picking automation, and we’re here to clear them up. Learn more in our blog.