Key Factors in Integrating Traditional and E-Commerce Order Fulfillment Operations
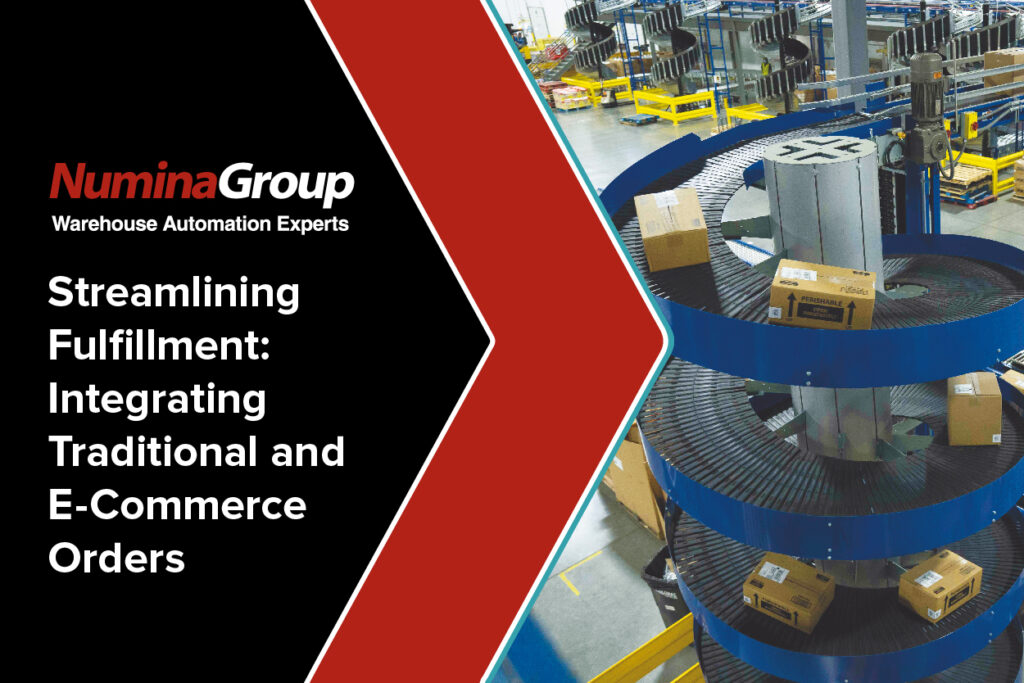
Adding e-commerce order fulfillment to an existing DC can be complex because e-commerce orders have a very different order profile than traditional B2B and retail store orders. Tips to consider.
Numina to Demonstrate RDS™ Warehouse Order Orchestration Suite at Modex 2024
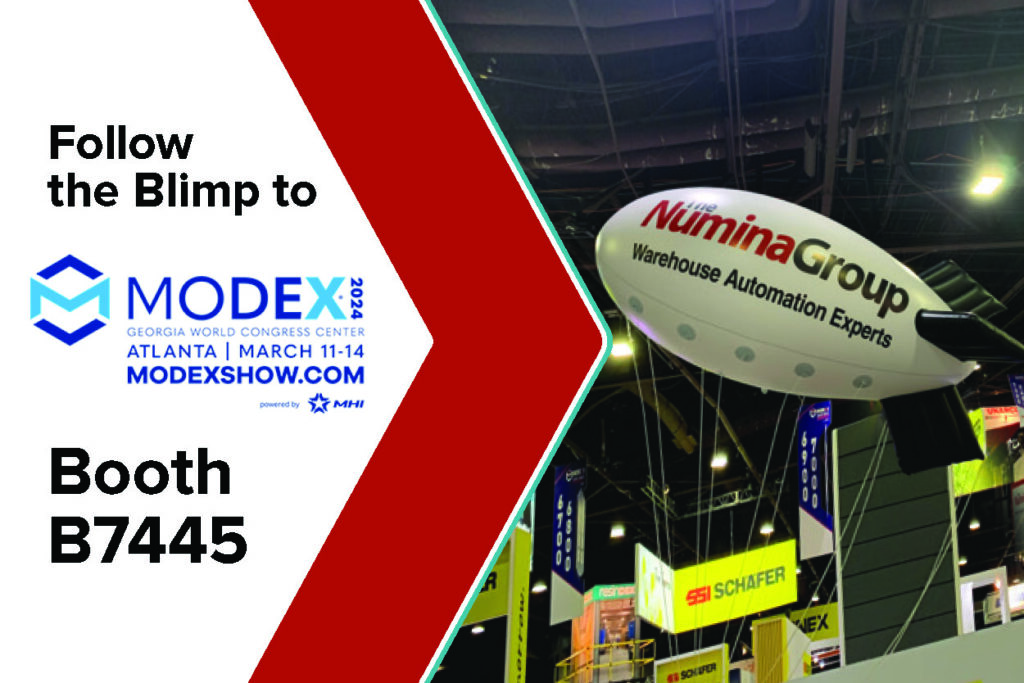
This year at ProMat, Numina featured a trifecta of warehouse automation solutions – RDS™ WES-WCS, Victory Voice™, and Pakt™. Learn more.
Warehouse Technologies to Consider NOW Before Your Next Peak Holiday Season
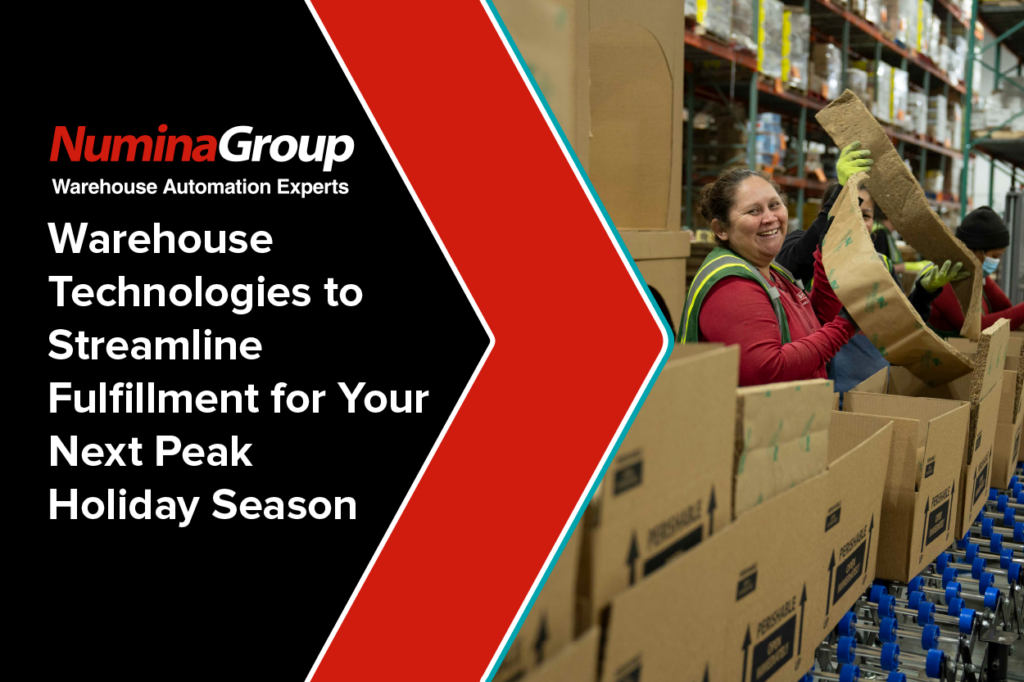
How well did your fulfillment operations keep up this past peak season? Is there room for improvement? Now is the time to consider warehouse technologies you can be deploy before the next peak season.
How End-to-End Warehouse Automation Can Future-Proof Your Company
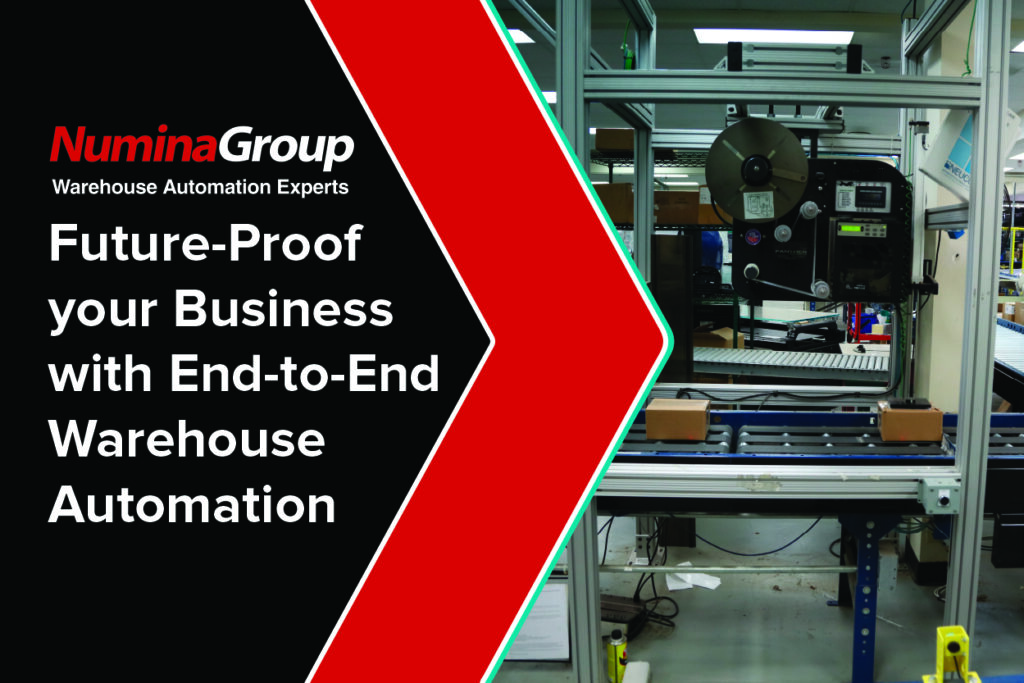
In a manual or partially automated warehouse, process improvements can boost throughput – but only to a point. Add these key warehouse technologies and you can double or triple productivity.
The True Cost of NOT Automating Your Warehouse
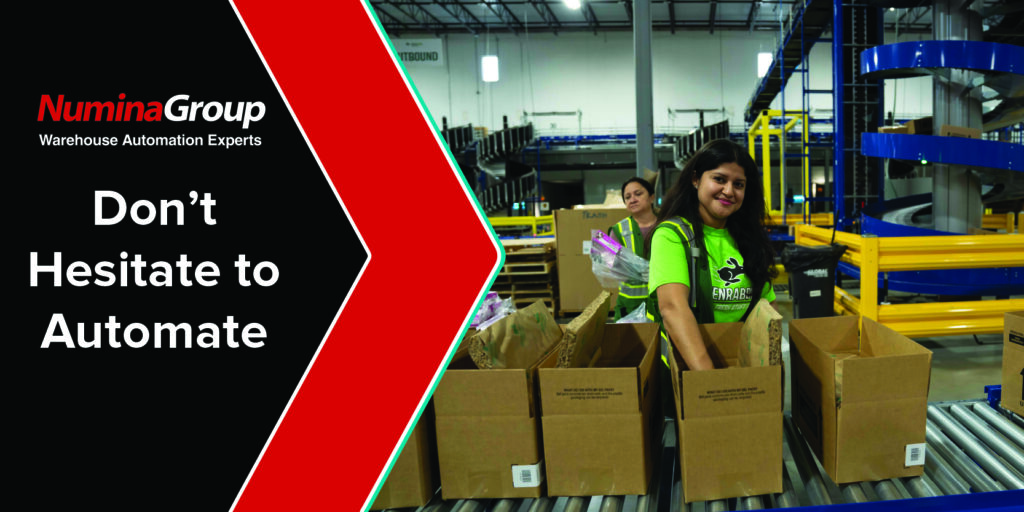
What are the costs of not automating your warehouse? In our blog, top factors & cost implications to consider as part of your total investment and ROI calculations.
Are You Ready for This Year’s Peak Shipping Season?
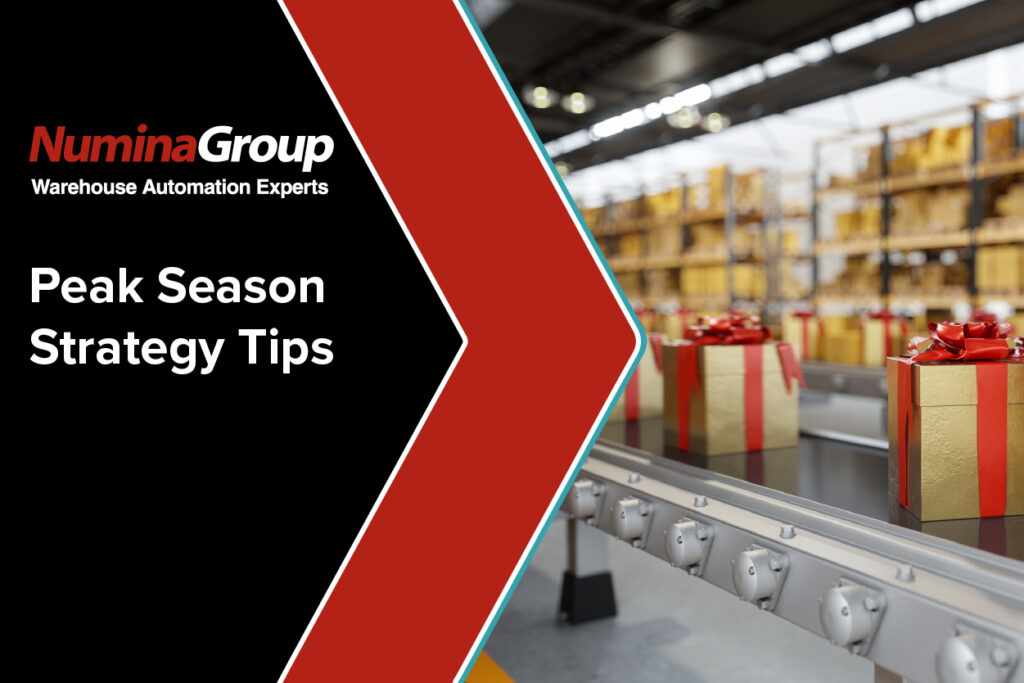
Is your fulfillment process able to provide seamless multichannel shopping? Tips to prepare now, with warehouse automation options for the future.
How Pick Modules and Zone Route Conveyors Keep Warehouse Pickers on Task
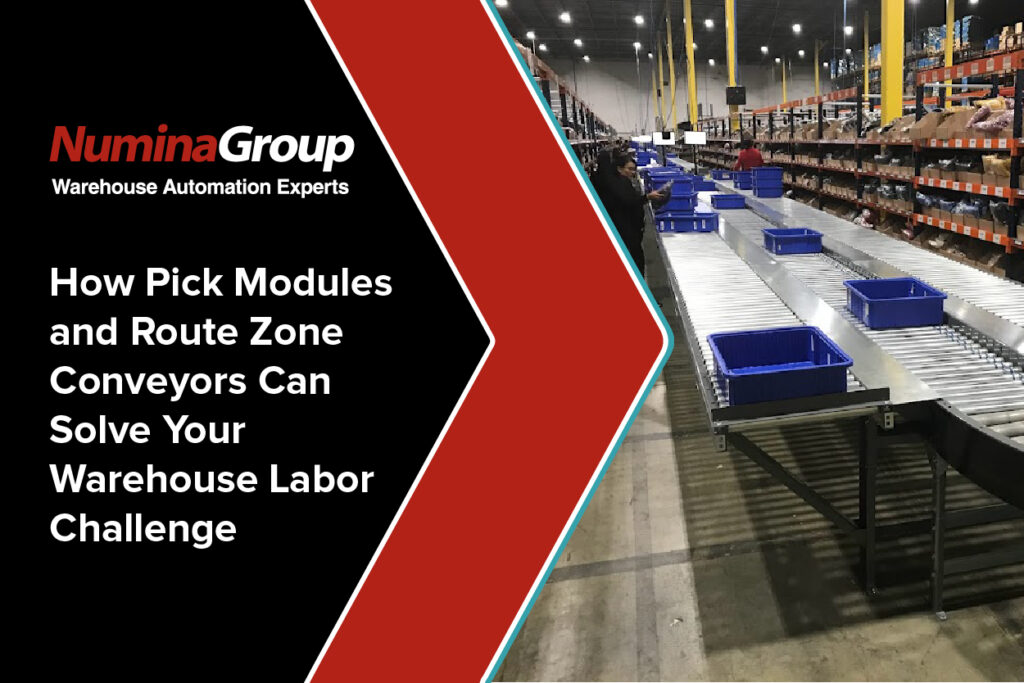
Extend the efficiencies gained with AMR-based picking to other areas of the warehouse. How Numina’s Pakt Print-and-Apply solution maximizes the benefits of AMR-based picking.
Lean Six Sigma Meets Warehouse Automation Design: A Winning Combination for Warehouse Optimization
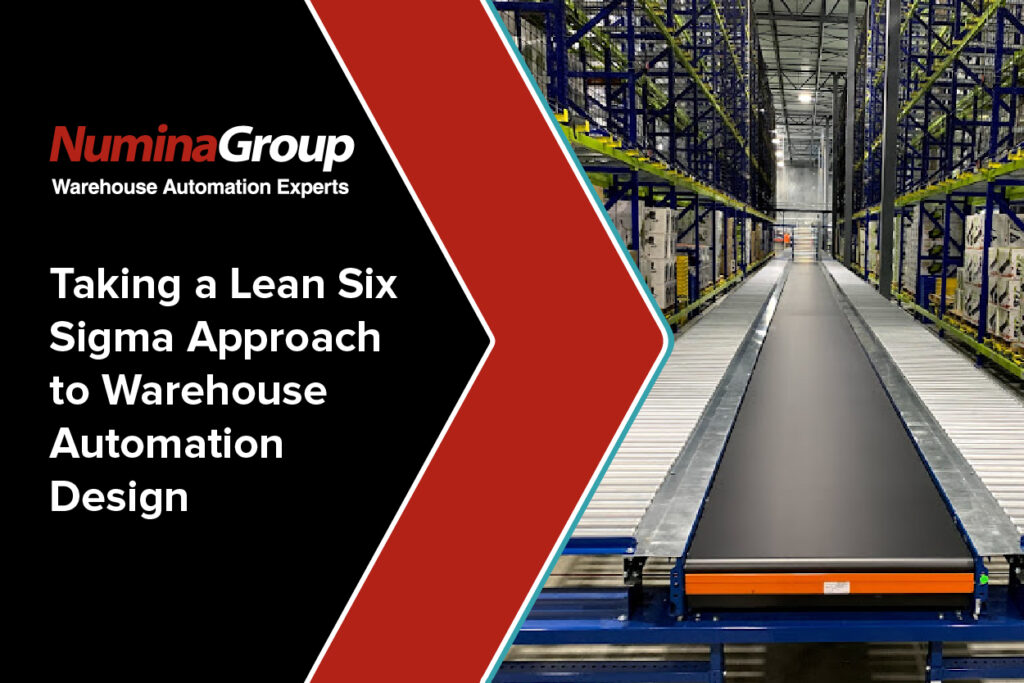
How to apply Lean Six Sigma concepts to improve warehouse processes or design a new facility for maximum efficiency & excellence in fulfillment.
The History of Goods to Person Systems
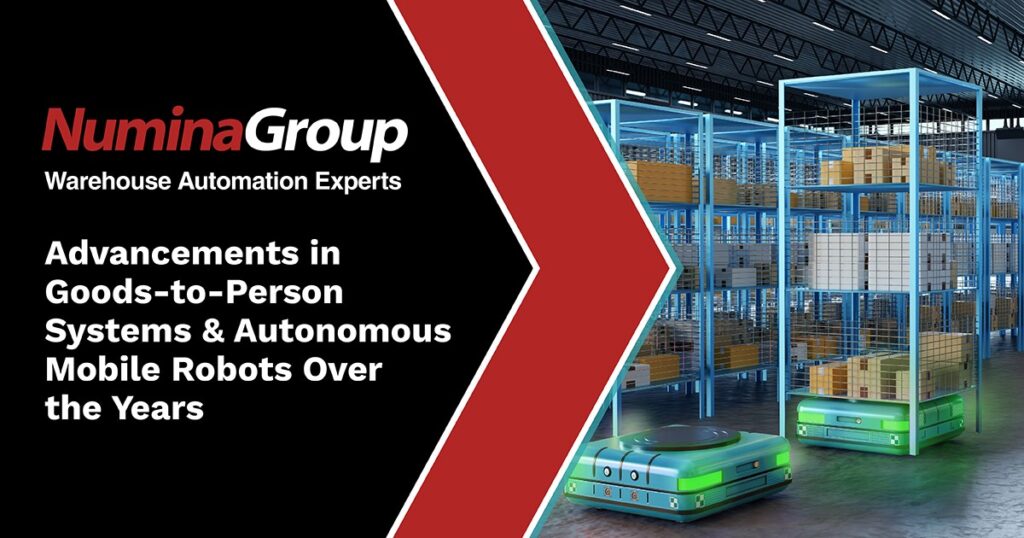
Learn about the evolution of goods-to-person (G2P) warehouse automation , advances in warehouse robots, and how efficient G2P can be.
3 Reasons Numina Group was the top booth to visit at ProMat 2023
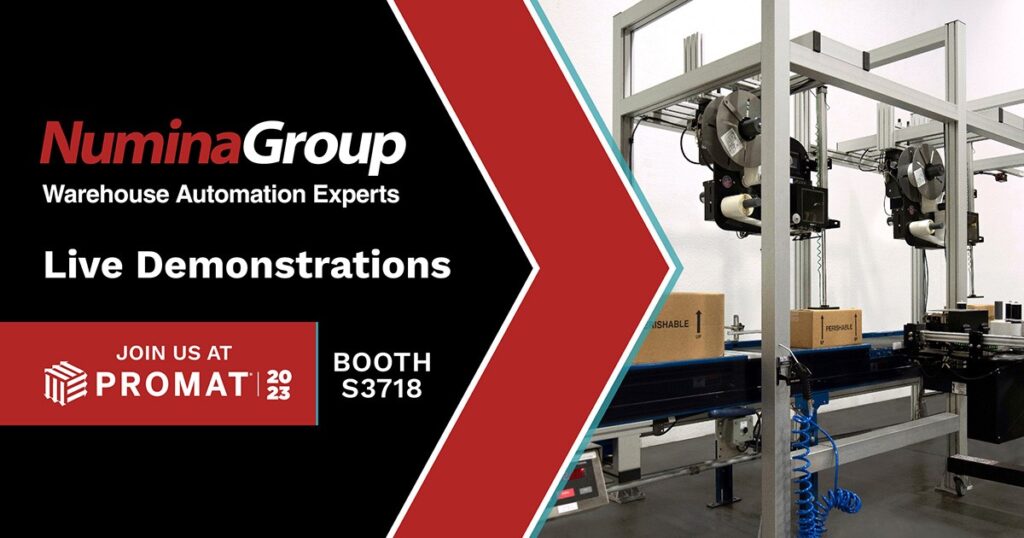
This year at ProMat, Numina featured a trifecta of warehouse automation solutions – RDS™ WES-WCS, Victory Voice™, and Pakt™. Learn more.