In a manual warehouse operation, it’s not unusual to rely on operators to manually select the carton size or polybag for packing orders.
This leads to excessive shipping and material costs due to the operator’s tendency to choose a larger-sized box than is necessary.
As a result, order packing, manifesting, and shipping operations become a bottleneck with multiple manual touches, wasted time and labor, excess void fill or air pillows, and higher carrier shipping rates.
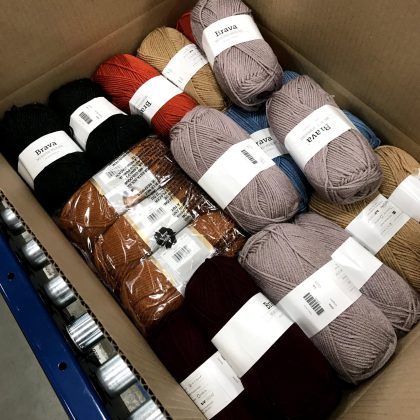