Pick to Light System
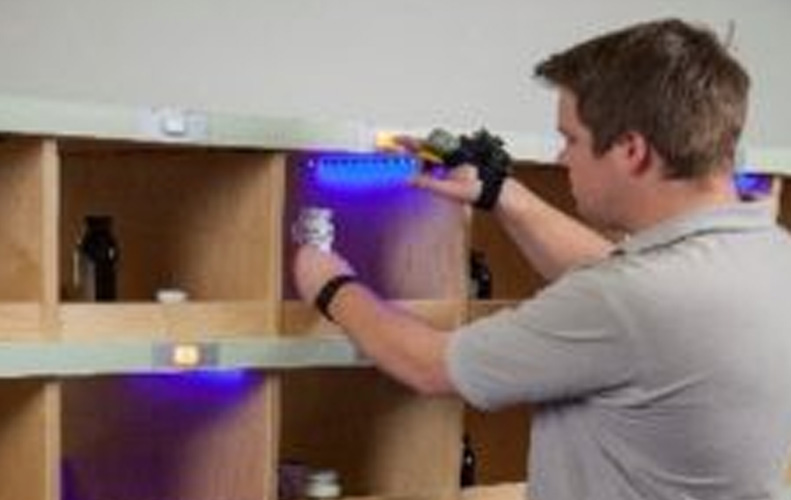
Put to Light Order Consolidation Pick to Light Systems, fast, simple, and accurate technology increases picking speed and lowers labor costs in case and each order fulfillment operations. Pick and Put to Light System benefits: Easy to install Simple to use Minimal operator training Fast and accurate compared to a paper or wireless terminal based…
Voice Picking Technology
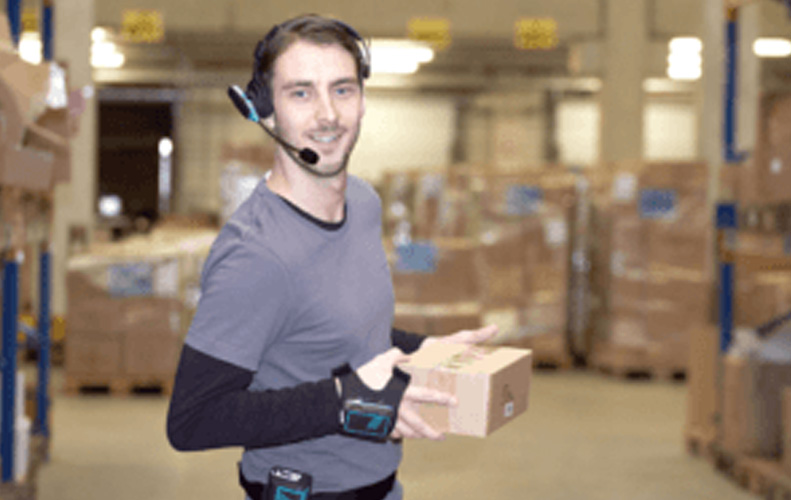
Innovations in Warehouse Design for Today’s Distribution Center Investing in a voice picking suite that includes a complete family of pre-developed picking and warehouse automation application modules results in more united and efficient distribution practices. The application software, called a voice suite, goes beyond voice only applications and blends voice directed picking and automation components…
Save Green in your Distribution Center with Green Packaging Solutions
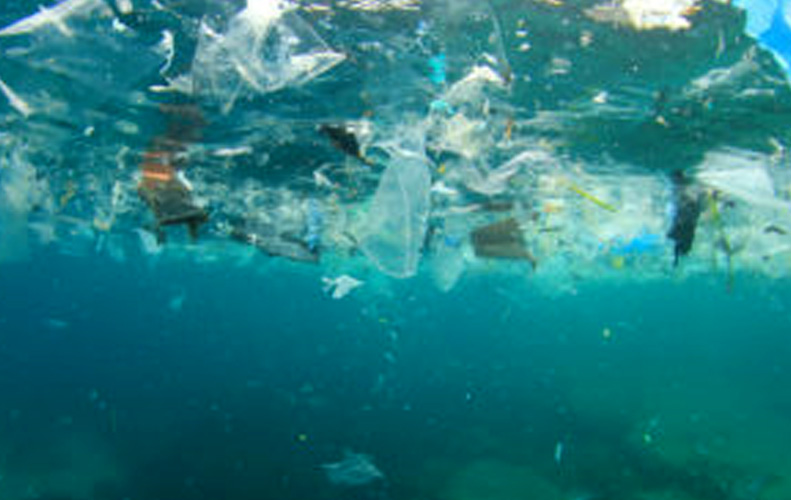
Numina Group’s Software and Technology to Reduce Waste and Wasted Steps with Green Packaging Solutions Corporate initiatives to reduce plastic consumption have captured significant media attention as of late, and while the merits of initiatives like eliminating plastic straws can be debated, excessive plastic consumption is a serious issue. Millions of tons of plastic waste…
Cartonization Software and Scan-Weigh-Dimensioning Technology
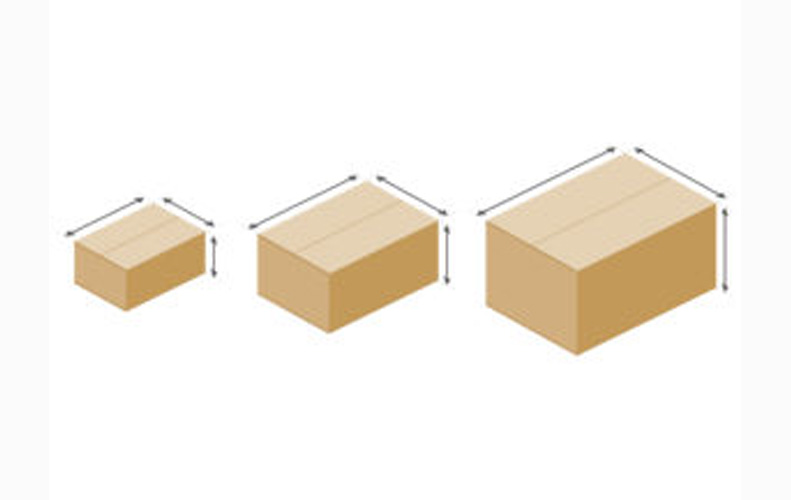
Increase Distribution Profitability UPS and FedEx both use dimensional weight to determine shipping rates, making it increasingly important for parcel B2B and B2C Internet fulfillment operations to use cartonization software and scan-weigh-dimensioning technology in order to have accurate inline dimension-weigh-capture performed for each outbound shipment. Estimating the dim-weight or relying on an operator to record…
Returning Customer Automation Distribution Success Story
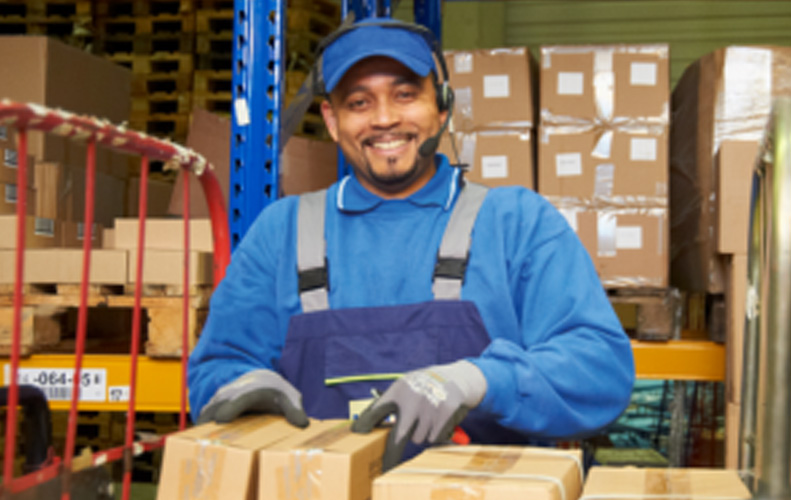
Returning customer and The Numina Group team up to design and imple
Retail Fulfillment Success Story
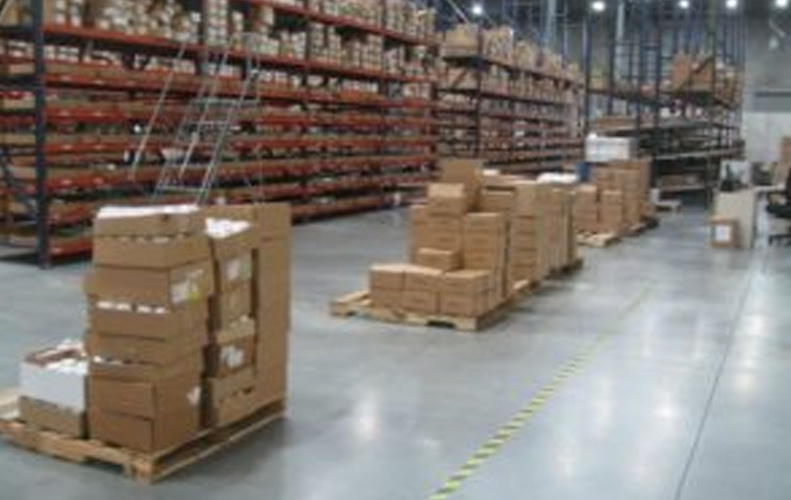
350,000 Sq. Foot Retail Fulfillment Distribution Center Streamlines the Picking Process by Moving to Pick by Voice for its 1,000,000 Active SKU’s When a leading retail fulfillment firm with over 250 retail stores wanted to ditch its paper picking process, it leap-frogged RF and went directly to voice picking, which turned out to be a…
Linux is Poised to Dominate Warehouse and Industrial Automation Software
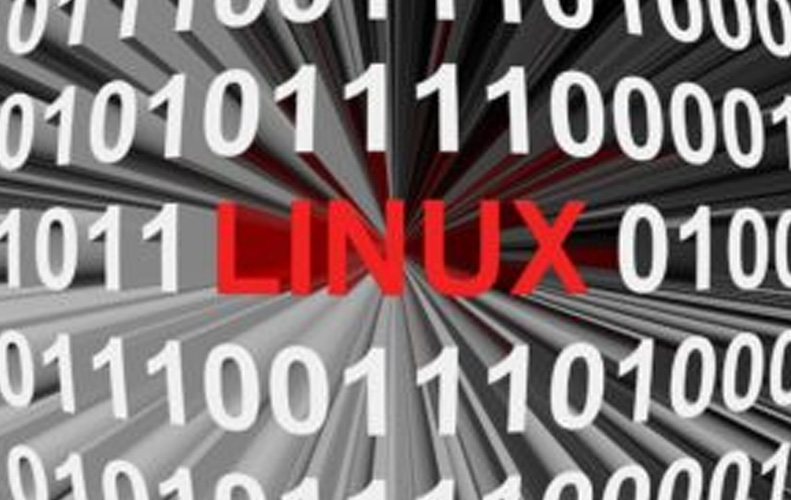
In 1991 Finnish student, Linus Torvald, had a vision: to create a new free operating system and Linux was born. If you include the millions of computer systems and embedded devices running its little brother Android, from phones, printers, home appliances, and mobile hand-held computers, Linux is now the world’s #1 operation system. In 1999,…
Accelerate Ecommerce Order Fulfillment
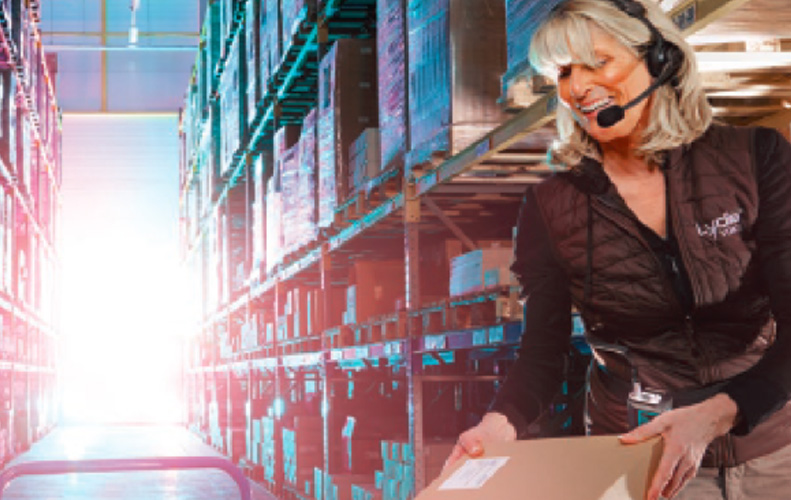
Accelerate Ecommerce Order Fulfillment Productivity by Automating the Last 100’ of the DC! We’re often asked by clients to identify ways to accelerate throughput and eliminate the bottlenecks in a manual pack and ship order fulfillment operation. The initiative can include all three components of Ecommerce Order Fulfillment – pick, pack, and ship at the…
Key Automation For Omnichannel Ecommerce Order Fulfillment Solutions
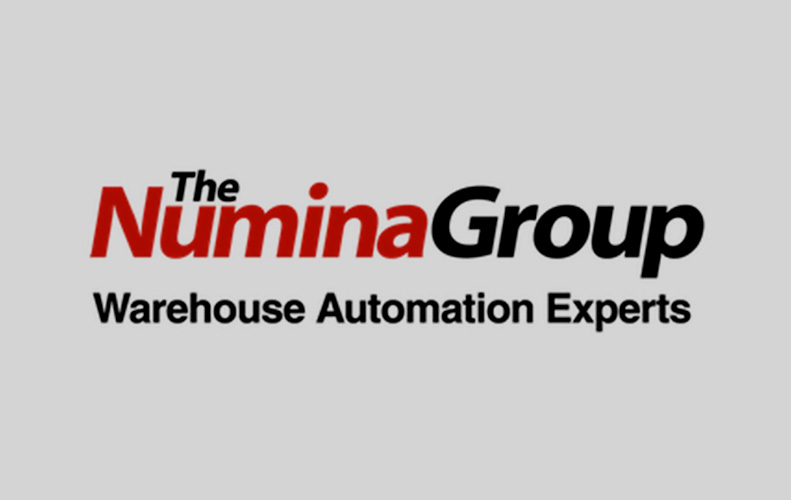
Customers are rapidly migrating to online order placement of goods for B2C or store pick-up. Customers have become accustomed to having their online goods delivered within a day or two. Companies are finding that in order to compete, they must invest in automation for omnichannel ecommerce fulfillment solutions. As a result, companies that provide their own…
Automation Off-sets Warehousing Labor Shortage
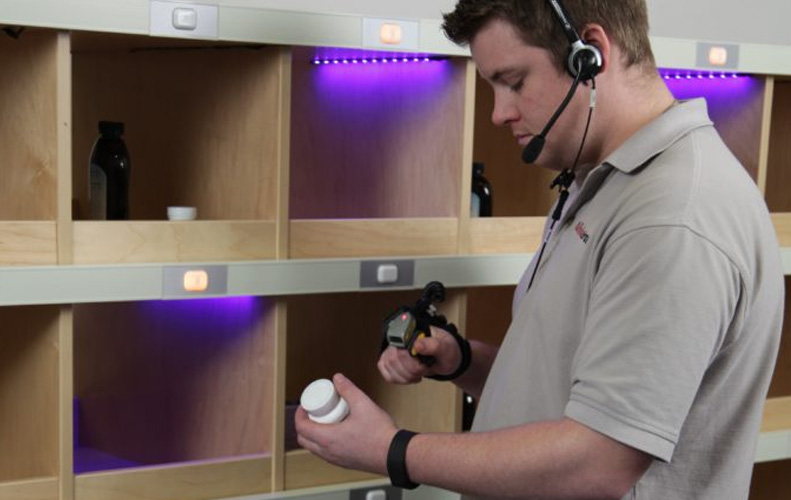
Unemployment recently hit a 10 year low, sending a wake-up call that companies need to invest in technology to increase productivity in warehousing and distribution operations! The US Job Market added more jobs than expected, lowering the US Unemployment rate to a 10-year low. The latest report shows the addition of 138,000 jobs with the…